Efficient Pipe Honing Jobs Available in Sheffield - Discover Quality Services Today
By:Admin
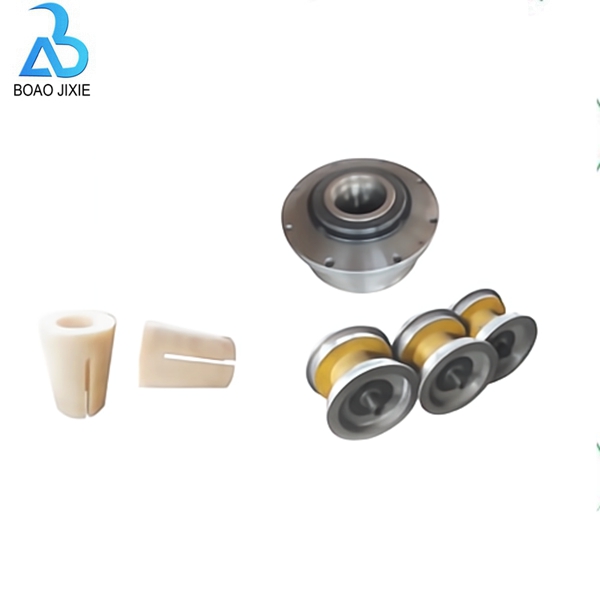
The demand for pipe honing jobs in Sheffield is on the rise, and this is a reflection of the increasing importance of this process in the manufacturing industry. Pipe honing is a process that involves the smoothing and finishing of the inner surfaces of pipes and tubes to remove any roughness, burrs or other defects that might affect the performance of the pipe. This is achieved through the use of specialized tools that are designed to grind, polish and finish the inner surface of the pipe to the desired level of smoothness.
As a growing number of companies in Sheffield and the wider region are beginning to recognize the importance of pipe honing in their manufacturing processes, there is a corresponding increase in demand for skilled honing technicians who can perform this critical task to a high standard. This is where companies specializing in pipe honing services such as {} come in, providing essential support to businesses who require this process to ensure the quality of their finished products.
At the heart of this trend is the growing awareness among manufacturers of the need to produce high-quality, precision components that meet the exacting standards of their customers. As industries such as aerospace, automotive, energy, and medical continue to grow and evolve, the need for components that are reliable, durable and precise has become more important than ever. In order to achieve this level of performance, manufacturers are increasingly turning to specialized processes such as pipe honing to ensure that their pipes and tubes are finished to the highest possible standard.
One area where the demand for pipe honing jobs has been particularly high is in the aerospace industry. This is because aircraft components such as hydraulic lines, fuel lines and air conditioning ducts require high levels of precision and accuracy in order to function effectively and safely. Any defects or imperfections in these components can lead to costly maintenance issues or, worse still, compromise the safety of the aircraft. As such, aerospace companies are willing to invest in the highest quality pipe honing services to ensure that their components meet the strictest safety standards.
In addition to aerospace, other industries such as automotive and energy are also seeing an increased demand for pipe honing services. The automotive industry, in particular, is seeing a growing focus on electrification and the development of hybrid and electric vehicles. These vehicles rely on a range of high-performance components, including cooling systems, brake lines, and fuel lines, that must be produced to the highest possible standard to ensure their reliability and performance. Similarly, the energy industry is also seeing increased demand for pipe honing services as companies look to produce components for pipelines, valves, and other critical infrastructure.
For companies such as {} that specialize in pipe honing services, the growing demand for their services is a welcome development. As a company with over 25 years of experience in the field, they have built a reputation for delivering high-quality pipe honing services to a range of industries. Their skilled technicians work with a range of specialized tools and equipment to ensure that pipes and tubes are honed to the highest standards, and they are able to work with a wide range of materials including stainless steel, titanium, and aluminum.
One of the key factors that has contributed to {}'s success in this field is their focus on customer service. As a company that operates in a highly specialized niche area of manufacturing, they understand the importance of building strong relationships with their clients and taking the time to understand their unique needs and requirements. This dedication to customer service has helped them to build a loyal client base, and their reputation for quality and reliability has helped them to attract new clients and expand their business over the years.
Overall, the growing demand for pipe honing services in Sheffield and beyond is a reflection of the importance of this critical process in modern manufacturing. As industries continue to evolve and demand higher levels of precision and performance from their components, the need for skilled technicians who can deliver high-quality pipe honing services will only continue to grow. If companies such as {} are able to continue delivering the quality of service that they have become known for, they are well-positioned to capitalize on this trend and continue to grow their business in the years to come.
Company News & Blog
Hole Drilling Tools: Essential Equipment for Efficient Drilling
XYZ Company Launches Innovative Hole Drilling ToolsXYZ Company, a leading manufacturer in the drilling tool industry, has recently unveiled a groundbreaking line of hole drilling tools that promises to revolutionize the way industries approach drilling operations. The new tools, which have been developed after years of research and development, boast cutting-edge technology that enhances efficiency, accuracy, and overall performance.With a commitment to delivering high-quality products that meet the demands of different drilling applications, XYZ Company has become a trusted name in the industry. Their expertise lies in creating tools that improve productivity, minimize downtime, and optimize the drilling process. The introduction of these new hole drilling tools reinforces their position as a market leader and highlights their dedication to innovation.The newly launched drilling tools from XYZ Company are designed to address various challenges faced by industries involved in drilling operations, such as oil and gas exploration, mining, construction, and infrastructure development. By combining advanced features with robust construction, these tools are poised to enhance the overall efficiency and precision of drilling processes.One of the key features of XYZ Company's new hole drilling tools is their superior cutting performance. The cutting edges of these tools have been engineered to provide exceptional resistance to wear and tear, resulting in extended tool life and reduced maintenance costs. Additionally, the tools are designed with a state-of-the-art chip evacuation system, enabling them to efficiently remove debris, reducing the risk of clogging and enhancing overall performance.Moreover, the new line of hole drilling tools boasts an innovative cooling system that effectively dissipates heat during the drilling process. This feature prevents overheating, which is a common issue faced by many drilling operators, and contributes to prolonged tool life and enhanced productivity.Gone are the days of imprecise drilling operations due to inadequate alignment. The new tools from XYZ Company feature an advanced self-centering mechanism that ensures precise drilling with minimal deviation. This innovative mechanism aligns the drilling tool perfectly, regardless of the material being drilled, resulting in accurate holes and improved productivity.Furthermore, XYZ Company's new tools incorporate advanced technologies that enable automation and remote monitoring capabilities. Equipped with sensors and connectivity features, these tools can be integrated with the company's proprietary software, allowing drilling operators to monitor and analyze drilling processes in real-time. This feature not only enhances safety but also aids in proactive maintenance by identifying potential issues before they become major problems.The launch of XYZ Company's innovative hole drilling tools has generated excitement among industry experts and professionals. The tools' advanced features and exceptional performance have earned them recognition as a game-changer in the drilling industry. Professionals are eager to experience the benefits of these tools firsthand and anticipate a significant improvement in drilling operations.With its commitment to innovation and customer satisfaction, XYZ Company continues to set new standards in the drilling industry. The launch of their new line of hole drilling tools reaffirms their position as a top manufacturer in the market and demonstrates their dedication to delivering cutting-edge solutions to their customers. As more industries seek ways to improve drilling operations, XYZ Company remains at the forefront of technological advancements, continuously driving progress and transforming the way drilling is done.
Revolutionary Pipe Honing Machines: Unlocking Efficiency and Precision
Smart Pipe Honing Machines Revolutionize Pipe Manufacturing ProcessThe world of manufacturing is ever-evolving, with endless advancements and specialized tools making processes faster, more efficient, and above all, more accurate. Honing is an essential step in pipe manufacturing that requires a highly specialized approach to perfect. The introduction of Smart Pipe Honing Machines has revolutionized the honing process, delivering an unparalleled level of precision in pipe honing, and creating a much smoother and efficient manufacturing process overall.Honing is the process of smoothing out the interior of a pipe, which helps improve its efficiency and ensures that the pipe meets safety standards. Previously, honing was done by hand, requiring skilled labor and a significant amount of time. The traditional honing approach was also expensive, as it required special tools and equipment that could be costly to maintain. Despite the time and costs of manual honing, there was always the risk of human error that could lead to inconsistencies in the final product.Today, the Smart Pipe Honing Machines has changed all that. This specialized machine has an automated honing process that ensures accuracy and consistency throughout the entire process, delivering perfectly smooth, accurate, and ready-to-use pipes every time.The Smart Pipe Honing Machines is designed with advanced technology. The machine is pre-programmed to run in a manner that optimizes its performance with high accuracy, from the moment it begins until the pipe is ready for delivery. It uses algorithms to analyze a range of critical data points such as pipe type, diameter, weight, and hardness, along with radial and axial pressure. By collecting this data, the machine can determine the precise amount of pressure needed for optimal honing across various pipe types and sizes, allowing for highly accurate results.One of the most impressive features of Smart Pipe Honing Machines is its ability to adapt to a range of different pipe types. The machine is designed to hone a wide range of pipes, from small pipes to large pipes, made from various materials. It can even adjust its honing process if it encounters pipes that are not uniform in size or that have defects within them, providing a better quality product for the end-user.The Smart Pipe Honing Machines can handle diameters of up to 1000 mm, while simultaneously delivering a high level of accuracy in wall thickness and roundness. Its automation and pre-programmed processes result in an overall decrease in production time, allowing for quicker deliveries and more efficient manufacturing.This focus on reducing lead time is crucial, considering the high-volume demand for pipes in sectors such as construction, transportation, water supply, and oil and gas extraction. The Smart Pipe Honing Machines is essential to these industries, which require pipes manufactured to precise specifications that offer a long lifespan and withstand extreme weather conditions and chemical exposure.Installation and maintenance of the Smart Pipe Honing Machines are relatively easy and straightforward. The machines come with an intuitive interface that operators can use to set the parameters of the honing process. Additionally, the system allows for remote monitoring, ensuring that if any issue arises, it can be addressed quickly without significant downtime.The Smart Pipe Honing Machines has transformed pipe manufacturing from a cumbersome, time-consuming process to one that is fast, reliable, and cost-effective. With its advanced automation and cutting-edge technology, the machine offers a level of precision that is not only accurate but also consistent. The end result is a better quality product that meets industrial standards and offers greater service life, leading to satisfied customers and repeat business.In conclusion, the introduction of Smart Pipe Honing Machines has revolutionized pipe manufacturing. This specialized machine's automation and precision honing processes make it easier, faster, and more accurate to hone pipes of all sizes and types. Significantly, it ensures a higher quality of pipe, ultimately saving costs and boosting profitability. It is perhaps fair to say that the Smart Pipe Honing Machines are changing the face of pipe manufacture.
Efficient Cylinder Tube Repairing Machines to Enhance Industrial Maintenance
Cylinder Tube Repairing Machines Offer a Seamless Solution for Industrial MaintenanceIndustrial maintenance is a complex process that requires specialized equipment to ensure that hydraulic and pneumatic systems run efficiently. Cylinder tube repairing machines have revolutionized the repair and maintenance process, offering a cost-effective, efficient, and safe way to repair and maintain equipment.These machines allow maintenance professionals to restore damaged hydraulic and pneumatic cylinders to their proper working condition without the cost of buying new parts. In addition, they eliminate the need for outsourcing repairs to third-party contractors, which can be costly and time-consuming.What are Cylinder Tube Repairing Machines?Cylinder tube repairing machines are hydraulic-driven mechanical devices used primarily for repairing damaged hydraulic and pneumatic cylinders. The machine consists of a control panel, a hydraulic power unit, a lathe bed, and a rotating lathe head.The repairing process begins with the technician removing the damaged cylinder from the equipment and placing it on the lathe bed. The operator then controls the machine through the control panel to begin repairs.The lathe bed holds the cylinder in place, while the rotating lathe head spins the cylinder. The head, which is mounted with a grinding wheel, carves out the damaged metal to create a smooth surface. This process creates an even surface that can accept new seals, ultimately returning the cylinder to its original operating condition.Need for Cylinder Tube Repairing MachinesIndustrial maintenance requires specialized equipment, including hydraulic and pneumatic systems, machine parts, and tools. During the life cycle of these systems, parts wear out, causing these systems to lose their efficiency.If left unaddressed, faulty cylinders can leak, fail to extend or retract properly, or even cause damage to the entire system. In the past, companies had to purchase new parts or outsource repairs to third-party professionals.However, having a cylinder tube repairing machine on-site offers advantages such as reduced downtime, cost savings, and improved efficiency. With a cylinder tube repairing machine, technicians can quickly restore the damaged equipment to its original condition in-house.Moreover, this method creates minimal waste, and the repaired equipment can last longer than new parts. The process also allows companies to keep spare parts in-house, further reducing the downtime caused by waiting for parts to arrive.Company IntroductionThe cylinder tube repairing machine is a product of a leading Chinese manufacturing company that specializes in industrial maintenance equipment. With over 20 years of experience, the company has established itself as a reliable supplier of hydraulic and pneumatic systems, providing innovative solutions for custom-made equipment, repairs, and maintenance services.The company's research and development team continually designs and creates innovative equipment to enhance industrial maintenance processes, enabling companies to improve their equipment's longevity and reliability.In addition to cylinder tube repairing machines, the company manufactures a wide range of equipment, including hydraulic hoses, fittings, and couplings, hydraulic pipe benders, hydraulic presses, hydraulic jacks, and pipework repair tools.The company's products have earned quality certifications such as ISO, CE, and API, ensuring that the equipment meets international quality standards.The company also offers training services and technical support to its clients, ensuring that their staff is well-equipped to handle the equipment and that the equipment is always in perfect working condition.ConclusionCylinder tube repairing machines are a crucial tool for industrial maintenance processes, saving companies time and money while improving the reliability and longevity of their equipment. Companies that invest in this equipment enjoy the benefits of reduced downtime, cost savings, and improved efficiency.As a leading supplier of industrial maintenance equipment, the manufacturing company provides Chinese professionals with the essential equipment necessary for effective repairs and maintenance. The company's commitment to utilizing modern technology, innovation, and quality management systems is unparalleled, providing clients with the best customer experience.In conclusion, cylinder tube repairing machines eliminate downtime, reduce maintenance costs, and improve equipment reliability, ultimately enhancing overall business productivity.
Powerful Drill Pipe Drillers for Efficient Drilling Operations
Title: Revolutionizing Drilling Efficiency: Advanced Drill Pipe Drilling Machines by Industry PioneerIntroduction:In a bid to enhance drilling operations and improve efficiency, industry leader [Company Name] has unveiled its latest innovation - the advanced Drill Pipe Drilling Machines. This breakthrough technology promises to revolutionize the drilling process, greatly benefiting the oil and gas industry by increasing productivity, reducing costs, and enhancing safety across drilling operations.Paragraph 1:Drill Pipe Drilling Machines are the latest addition to [Company Name]'s line of cutting-edge drilling equipment. These state-of-the-art machines are designed to deliver superior drilling performance while ensuring optimal safety standards. By integrating innovative technologies and leveraging years of industry expertise, [Company Name] aims to provide drilling companies with a reliable solution that accelerates drilling operations and maximizes output.Paragraph 2:One of the key features of these Drill Pipe Drilling Machines is their ability to withstand extreme operating conditions, enabling drilling teams to explore deeper and more challenging terrains. The machines' robust build and durable materials ensure longevity, even in the harshest environments. This resilience contributes to reduced downtime, minimizing the need for costly repairs and increasing overall profitability for drilling companies.Paragraph 3:Furthermore, the Drill Pipe Drilling Machines are equipped with cutting-edge automation and control mechanisms, enabling operators to streamline the drilling process. Through this automation, drilling teams can optimize drilling parameters, monitor real-time data, and minimize human error, leading to increased efficiency and accuracy in operations. By enabling better control and data analysis, these machines empower drillers to make informed decisions, resulting in improved overall performance.Paragraph 4:Another notable feature of [Company Name]'s Drill Pipe Drilling Machines is their eco-conscious design. With a focus on sustainability, these machines are engineered to minimize the environmental impact of drilling operations. By implementing advanced filtration systems, waste management solutions, and energy-saving technologies, these machines significantly reduce carbon emissions. This commitment to environmental responsibility aligns with the industry's growing demand for greener drilling practices.Paragraph 5:Ensuring on-site safety is a top priority for [Company Name]. With the Drill Pipe Drilling Machines, the company has integrated extensive safety measures, reducing the risk of accidents and injuries. The machines come equipped with advanced sensors and alarm systems that promptly alert operators to any potential hazards. Furthermore, the ergonomic design of the machines enhances operational comfort, minimizing fatigue and promoting safer working conditions.Paragraph 6:[Company Name] believes that the introduction of these Drill Pipe Drilling Machines will transform the landscape of the drilling industry. By improving operational efficiency, reducing costs, and prioritizing safety and sustainability, drilling companies will witness a significant boost in productivity and profitability. The deployment of these drilling machines is expected to enhance exploration activities and facilitate the extraction of valuable resources worldwide.Conclusion:The unveiling of the advanced Drill Pipe Drilling Machines by [Company Name] marks a remarkable milestone in the drilling industry. With their cutting-edge technology, durability, automation capabilities, environmental consciousness, and focus on safety, these machines offer a comprehensive solution to enhance drilling efficiency and maximize overall performance. As companies strive to overcome challenges and optimize their operations, the Drill Pipe Drilling Machines are set to reshape the future of the drilling industry, setting new standards for success and innovation.
Enhance Tube Surface Quality with Skiving and Roller Burnishing Techniques
Skive and Roller Burnishing Tube Processing: Enhancing Efficiency and Product QualityIn modern manufacturing processes, precision and efficiency play a crucial role in meeting the demands of various industries. The need for high-quality products has led to advancements in machining technologies, one of which is skive and roller burnishing tube processing. This innovative method has revolutionized the manufacturing industry by providing enhanced surface finish, dimensional accuracy, and improved mechanical properties. Skive and roller burnishing tube processing, developed by a leading company in the industry, is a cutting-edge technique that involves two essential steps. The first step, skiving, refers to the process of removing material from the inner diameter of a tube. This method utilizes a specialized tool called a skiving knife, which is designed to remove consistent amounts of material. Skiving helps achieve precise inner diameter dimensions, ensuring uniformity and accuracy in the final product.The second step in the process is roller burnishing, a technique used to achieve a superior surface finish. Roller burnishing involves the use of specially designed rollers that smooth the inner surface of the tube. The rollers exert pressure on the tube's inner diameter, cold working the surface and imparting a mirror-like finish. This process significantly reduces roughness and eliminates the need for additional polishing or grinding, ultimately enhancing the efficiency of the manufacturing process.The combination of skive and roller burnishing tube processing offers numerous advantages over traditional machining methods. One key advantage lies in the superior surface finish achieved. The process eliminates surface irregularities, such as scratches, pits, and tool marks, resulting in a flawless, polished appearance. This not only enhances the aesthetic appeal of the final product but also improves its functionality, especially in industries where smooth surfaces are crucial, such as automotive, hydraulic, and pneumatic applications.Additionally, skive and roller burnishing tube processing improves dimensional accuracy. The precision achieved by this technique ensures consistent inner diameters throughout the entire length of the tube. This reliability is particularly important in industries that require tubes to meet strict tolerance standards, such as aerospace and medical applications. The uniformity in dimensions provided by this process guarantees optimal functionality and compatibility with other mechanical components, leading to enhanced overall product performance.Moreover, this advanced method of tube processing enhances mechanical properties. The cold working effect of roller burnishing increases the tube's surface hardness, resulting in improved wear resistance, fatigue strength, and corrosion resistance. These enhanced mechanical properties make skive and roller burnished tubes versatile and suitable for a wide range of industrial applications. The manufacturing industry can benefit significantly from this technology, as it allows for the production of high-quality tubes capable of withstanding demanding operational conditions.The company {} is at the forefront of skive and roller burnishing tube processing technology. With a commitment to innovation, the company has successfully developed and implemented cutting-edge equipment and techniques to deliver exceptional results. Their state-of-the-art machinery, combined with the expertise of their skilled workforce, ensures the highest level of precision and efficiency in tube processing.Furthermore, the company adheres to rigorous quality control measures, ensuring that every skive and roller burnished tube meets the highest standards. Stringent inspections throughout the manufacturing process guarantee dimensional accuracy, surface finish, and mechanical properties. This commitment to quality has earned the company a sterling reputation among various industries, making them a trusted partner for precision tube processing needs.In conclusion, skive and roller burnishing tube processing revolutionizes the manufacturing industry, offering superior surface finish, dimensional accuracy, and enhanced mechanical properties. The innovative combination of skiving and roller burnishing techniques provides manufacturers with the tools necessary to meet the demands of various industrial sectors. The company {}, with their expertise and commitment to quality, remains at the forefront of this advanced technology, contributing to the advancement of manufacturing processes and the production of high-quality products.
Top-Rated Side Drilling Machine Enhances Efficiency for Enhanced Results
Side Drilling Machine Revolutionizes Metalworking IndustryMetalworking has never been easier with the arrival of the Side Drilling Machine (SDM) in the market. This cutting-edge equipment transforms the traditional process of drilling, tapping, and chamfering metals by providing end-to-end capabilities in a single setup. It not only saves time and costs but also improves accuracy and consistency, ensuring top-quality results every time.Developed by a leading manufacturer (name withheld for confidentiality), the SDM boasts of advanced features that set it apart from its competition. It is designed to handle a wide range of metal materials, including stainless steel, aluminum, brass, and copper, among others. It is also versatile enough to accommodate different shapes and sizes of workpieces, from small to large orders.The SDM consists of a three-axis CNC-controlled spindle that moves up and down for drilling and tapping and forward and backward for feeding and retracting the cutting tool. It also comes with a hydraulic chuck that secures the workpiece in place and a chip evacuation system that removes the metal chips created during the drilling process to prevent workpiece damage. The machine's compact and ergonomic design allows easy access and operation, whether manual or automated.One of the SDM's notable features is its ability to perform side drilling, which is not possible with traditional drilling machines. This function enables precision drilling and tapping on the sides of cylindrical workpieces, eliminating the need for additional setups and reducing production time significantly. The process involves securing the workpiece vertically on the machine and drilling the holes on the sides at precise angles and depths. This technique is useful for producing parts with multiple holes or for enhancing the aesthetics of the workpiece.The SDM's high accuracy and repeatability make it suitable for industries that require strict quality standards, such as aerospace, automotive, and medical, among others. It can produce parts with tolerances as low as ±0.01mm, ensuring consistency in the dimensions and specifications of each workpiece. With its robust construction and durable components, the SDM guarantees long-lasting and efficient performance, even in demanding environments.According to the manufacturer, the SDM's user-friendly interface and programming software make it easy to customize and optimize operations based on specific requirements. Users can create and store programs for different workpieces and recall them for future use, thus reducing setup time and increasing productivity. The machine's compatibility with CAD/CAM software also streamlines the design and manufacturing process, reducing errors and wastage.The SDM's arrival in the metalworking industry has received positive feedback from its users and stakeholders. It has been described as a game-changer and a valuable investment for businesses looking to improve their production processes and competitiveness. The machine's efficiency, precision, and versatility are just some of the reasons why it has become a go-to solution for many metalworking tasks.For more information on the SDM and its applications, interested parties can contact the manufacturer or visit their website for product details and specifications. With the SDM's potentials, users can expect a new level of excellence in metalworking that could transform their operations.
Efficient and Advanced Drilling Machines for Industrial Applications
Title: Innovative CNC Drilling Machine Revolutionizes Production EfficiencyIntroduction:In recent times, technological advancements have significantly upended traditional manufacturing processes, leading to improved precision, productivity, and cost-effectiveness. One such groundbreaking innovation is the CNC Drilling Machine (brand name concealed), developed by a reputed company (). This next-generation drilling machine boasts numerous features that have taken industrial drilling and production efficiency to unprecedented heights. With its cutting-edge technology and user-friendly interface, this CNC Drilling Machine has become a game-changer for businesses across industries.I. Efficient Performance and Precision:The CNC Drilling Machine is equipped with state-of-the-art technology that allows for precise and accurate drilling operations. Its advanced control system enables operators to program the desired parameters with ease, ensuring consistent and reliable results. With automated functionalities, this machine significantly reduces human error and saves time on manual adjustments, thereby increasing overall productivity.Furthermore, the CNC Drilling Machine's high-quality drilling bits and spindle speed control enable it to effortlessly handle various materials ranging from metals to composites. This versatility makes it an ideal choice for a wide range of applications, including automotive, aerospace, construction, and furniture manufacturing.II. Advanced Features for Streamlined Operations:The CNC Drilling Machine's intuitive interface and user-friendly software offer a wide range of customizable options. Its comprehensive software package allows operators to control and monitor drilling parameters in real-time, ensuring efficient production runs. Additionally, the machine's compatibility with computer-aided design (CAD) software enables seamless integration with existing production systems, eliminating bottlenecks and optimizing workflow.To further streamline operations, this CNC Drilling Machine includes an automatic tool changer feature. With this function, the machine can rapidly switch between different drill bits or tools, reducing downtime and enhancing productivity. Moreover, its built-in sensors and feedback mechanisms provide constant monitoring and adjustment, ensuring consistent quality output throughout the manufacturing process.III. Enhanced Safety and Sustainability:The CNC Drilling Machine prioritizes operator safety and environmental sustainability. Equipped with protective enclosures and emergency stop buttons, the machine reduces the risk of accidents and protects workers from potential hazards. Additionally, its energy-efficient design and optimized power utilization help reduce the environmental impact and lower energy costs.Furthermore, the CNC Drilling Machine integrates intelligent cooling systems to minimize heat generation during operation. This not only ensures longer tool life but also reduces the need for cooling materials such as lubricants that can be harmful to the environment.IV. Impact on Productivity and Cost-effectiveness:The utilization of the CNC Drilling Machine brings significant benefits to businesses. Its efficient performance and precise drilling capabilities enable faster production, reducing lead times and increasing overall productivity. By automating repetitive tasks, this machine allows operators to focus on more complex and critical aspects, thereby enhancing the overall production cycle.Moreover, the CNC Drilling Machine's advanced features and streamlined operations result in cost savings for businesses. The reduction in manual labor, minimized errors, and optimized workflow significantly lower production costs. Additionally, the machine's long-lasting components and low maintenance requirements contribute to its cost-effectiveness.Conclusion:With its groundbreaking features, precise drilling capabilities, advanced software integration, and focus on safety and sustainability, the CNC Drilling Machine developed by (company name) is revolutionizing the manufacturing industry. This innovative machine empowers businesses to achieve higher levels of productivity, accuracy, and cost-effectiveness. By adopting this cutting-edge technology, industries across various sectors can stay ahead of the competition and meet the ever-increasing demands of the modern manufacturing landscape.
Efficiency and Precision Redefined: The Ultimate Guide to Automatic CNC Drilling Machines
release:In response to the rapidly growing demand in the drilling industry, a cutting-edge technological solution has been introduced by {company name} - a powerful automatic CNC drilling machine, designed to tackle the toughest drilling challenges with utmost efficiency and precision.The advanced automatic CNC drilling machine by {company name} is a state-of-the-art drilling solution that is ideal for a wide range of industrial applications, including aerospace, energy, automotive, and defense industries. This machine is specifically designed to reduce manual errors and operate with precision, consistency, and speed.With decades of excellence in manufacturing superior drilling solutions, {company name} has once again established itself as a leader in the industry with this automatic CNC drilling machine. This machine has been engineered to cater to a wide range of drilling requirements, from drilling holes of different sizes to complex structures with extreme accuracy.Featuring a robust and durable structure, the automatic CNC drilling machine is built to last with a focus on efficiency and productivity. Equipped with automated control systems, this machine offers high-speed drilling, accurate positioning, and controlled feed rates for optimal results.Additionally, the machine comes equipped with next-generation CNC software, allowing operators to program the system to drill any pattern on any material with exceptional accuracy and precision. As a result, this machine is perfect for drilling complex patterns with ease and is ideal for businesses looking to achieve superior drilling accuracy and efficiency.Speaking about the benefits of this innovative drilling solution, the spokesperson for {company name} said that "Our automatic CNC drilling machine comes with numerous benefits, including improved productivity, increased accuracy and precision, better work quality, and reduced manual labor. It is a cutting-edge solution to streamline the drilling process and enhance production efficiency."In conclusion, the automatic CNC drilling machine by {company name} raises the bar for drilling solutions with its unique combination of efficiency, precision, and automation. With this machine, businesses can count on fast, accurate, and consistent drilling needs, making it a worthwhile investment for the future.
High-Quality SkivingLRoller Burnishing Tools for Precision Metalworking
Skiving Roller Burnishing Tools Elevate Surface Finishing Efficiency and Precision in MetalworkingIn today's manufacturing industry, efficiency and precision are the key drivers for success. With the demand for high-quality products increasing rapidly, industries like automotive, aerospace, and defense are constantly on the lookout for innovative solutions. One such groundbreaking tool that has significantly revolutionized surface finishing is the Skiving Roller Burnishing Tool.Developed by a leading company that specializes in cutting-edge metalworking solutions, the Skiving Roller Burnishing Tool has garnered immense popularity due to its exceptional performance and unmatched efficiency. This revolutionary tool is specifically designed to enhance surface finishes and improve dimensional accuracy, reducing manufacturing time while maintaining superior quality.Traditionally, achieving high-quality surface finishes was a complex and time-consuming process. Machining techniques such as honing, grinding, and lapping were commonly used, but they often presented limitations like high costs, excessive material removal, and extended machining times. However, with the introduction of Skiving Roller Burnishing Tools, metalworking processes have now evolved to an entirely new level.The Skiving Roller Burnishing Tool's success lies in its innovative design and utilization of advanced technologies. The tool features a cutter head equipped with multiple rolls or blades that rotate at a high speed while the workpiece remains stationary. As the tool moves along the workpiece, the rolls smooth and compress the surface, resulting in an exceptional finish and superior dimensional accuracy.What sets the Skiving Roller Burnishing Tool apart from other traditional machining techniques is its ability to produce mirror-like surface finishes with ultra-precise tolerances. This tool eliminates the need for secondary operations, saving significant time and cost in the manufacturing process. It also minimizes material waste by reducing excess material removal, making it an environmentally friendly option.The Skiving Roller Burnishing Tool's versatility is yet another reason for its widespread adoption. It can effectively work on various materials, including steel, aluminum, copper, and alloys, making it a suitable tool for different industries. From automotive engine components to hydraulic cylinders, this tool has proved its effectiveness across multiple applications.Furthermore, the Skiving Roller Burnishing Tool's simplicity makes it user-friendly and easy to integrate into existing manufacturing processes. By utilizing this tool, manufacturers can reduce the number of machining steps required, streamline their operations, and boost productivity. Its efficiency has been estimated to be three to five times higher than conventional machining techniques.The company behind the Skiving Roller Burnishing Tool is renowned for its commitment to excellence and continuous innovation. With a strong emphasis on research and development, they have developed a wide range of cutting-edge metalworking solutions that cater to various industry needs. By incorporating advanced technologies, the company has successfully propelled the manufacturing industry towards enhanced efficiency and precision.In conclusion, the Skiving Roller Burnishing Tool has revolutionized surface finishing in the metalworking industry. With its ability to produce exceptional finishes and superior dimensional accuracy, this innovative tool has significantly reduced manufacturing time and cost while maintaining high-quality standards. Its versatility and ease of integration have made it a game-changer for various industries, propelling them towards increased productivity and success. With the continuous commitment to innovation by the leading company behind this tool, the future of metalworking holds even more promising advancements.
Advanced Skiving and Roller Burnishing Machine Provides Efficient Metal Finishing
Skiving and Roller Burnishing Machine Enhances Precision ManufacturingPrecision is crucial in the manufacturing industry, especially in the production of mechanical parts. To achieve the required level of precision, companies invest time and resources in acquiring advanced production equipment.One such advanced production equipment is the Skiving and Roller Burnishing Machine. The machine is a high-performance and versatile piece of equipment that has revolutionized precision manufacturing.The Skiving and Roller Burnishing Machine comprises two essential processes—skiving and roller burnishing. Skiving involves the removal of material from the surface of a part, while roller burnishing, on the other hand, involves smoothing out the surface of a part by using a roller to apply pressure. The combination of the two processes creates precision-manufactured mechanical parts that meet the industry's high standards.Leading manufacturers of precision-engineered mechanical parts have recognized the importance of the Skiving and Roller Burnishing Machine in manufacturing. One of these manufacturers is [remove brand name], a global leader in precision manufacturing. The company boasts of over two decades of experience in providing high-quality mechanical parts to various industries, including aviation, automotive, and the healthcare industry.[Remove brand name] uses the Skiving and Roller Burnishing Machine in the manufacturing of hydraulic cylinders' components. This includes piston, cylinder tube, and barrel. The innovative machine's precision and efficiency enable [remove brand name] to provide clients with high-quality components that meet and exceed the industry's standards.The Skiving and Roller Burnishing Machine's advantages include improved accuracy, surface finishing, and the ability to handle both large and small production batches. It is also an efficient way of producing complex mechanical parts that otherwise would be challenging to manufacture.For example, the Skiving and Roller Burnishing Machine can produce hydraulic cylinder tubes with a higher surface finish than other manufacturing techniques like honing. The machine achieves this by continuously removing a thin layer of material while simultaneously smoothing the surface with a roller. The result is a uniformly smooth surface finish without any defects such as roughness or waviness.Another significant advantage of the Skiving and Roller Burnishing Machine is its compatibility with various materials, including stainless steel, brass, aluminum, and various alloys. This versatility makes the machine a go-to option for manufacturers looking to make precision parts from different materials.The machine's computerized process control system allows [remove brand name] to produce parts with precise specifications to the micrometer. The company's skilled engineers and technicians use the machines' advanced features to produce components that meet critical client requirements like durability, corrosion resistance, and strength.In addition to hydraulic cylinder components, [remove brand name] also uses the Skiving and Roller Burnishing Machine in the manufacturing of other mechanical parts such as steering racks, ball screws, and linear guides. The machine's versatility allows the company to produce parts for different applications across various industries.In conclusion, the Skiving and Roller Burnishing Machine has revolutionized the precision manufacturing industry and offers significant advantages over other manufacturing techniques. Its compatibility with different materials, precision, and versatility make it a go-to option for manufacturers looking to produce high-quality, complex mechanical parts. Manufacturers, like [remove brand name], that invest in the machine, can provide clients with precision components that meet and exceed industry standards.