Understanding the Definition and Importance of Deep Hole Drilling Machines
By:Admin
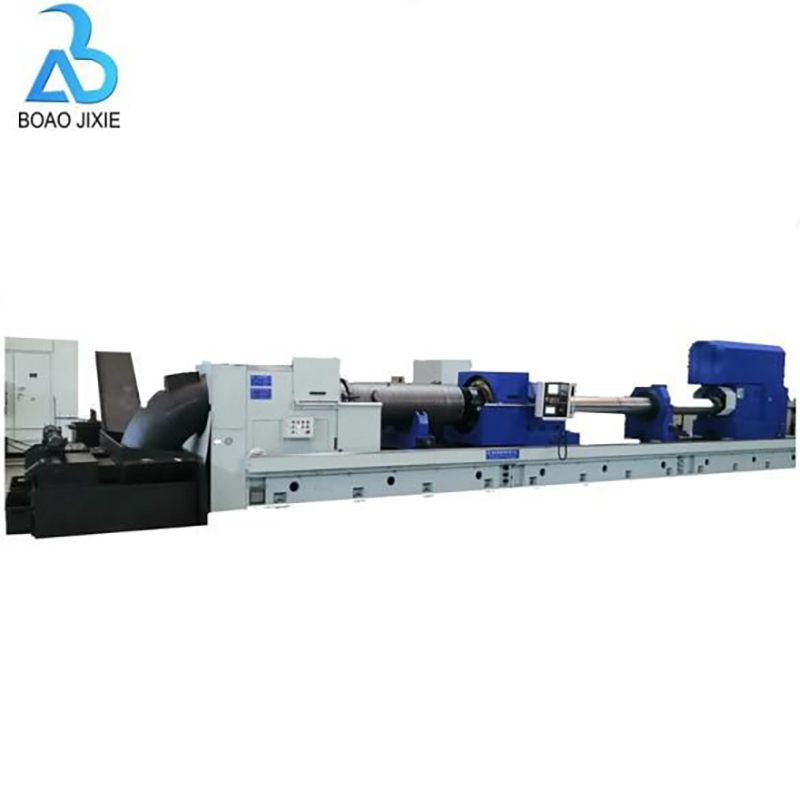
The manufacturing industry is constantly evolving, with new technologies and machines being developed every day to make industrial processes more efficient and cost-effective. One such technology that has gained significant popularity in recent years is deep hole drilling. Deep hole drilling refers to the process of drilling deep, narrow holes into a workpiece, typically at a depth-to-diameter ratio of greater than 10:1.
Deep hole drilling has become increasingly important in the manufacturing industry due to its ability to create high-precision, complex parts that are essential in various industries, including aerospace, defense, medical, and oil and gas. The process involves the use of a deep hole drilling machine, a highly specialized piece of equipment designed specifically for this purpose.
However, while deep hole drilling machines have a significant impact on the manufacturing industry, not all of them are created equally. The machine which doesn’t need to be named, stands out in the industry, thanks to its cutting-edge technology and innovative features.
Overview of the Deep Hole Drilling Machine
The {unnamed} deep hole drilling machine is a state-of-the-art, fully automated machine that is designed to meet the diverse needs of the manufacturing industry. It is equipped with features that offer increased accuracy and productivity, making it ideal for producing high-quality, precision parts.
The machine is built with a rigid structure and is equipped with an advanced hydraulic system, which ensures excellent stability during operation. It also features a robust spindle unit and a chip removal system that keeps the work area clean and free of debris.
The machine’s control system is fully automated, which means that the operator can easily program and control the drilling process as per the specific requirements of the workpiece. The intuitive interface and user-friendly controls make it easy for operators to use the machine, even if they have no prior experience with deep hole drilling.
Furthermore, the machine is designed to be versatile and can produce a wide range of parts, including long and small diameter holes, gun drilling, and BTA drilling. This makes it a valuable investment for any company that needs to produce high-precision parts with complex geometries.
Company Introduction
{Un-named} is a leading manufacturer of deep hole drilling machines and has been in the industry for more than three decades. The company is known for its cutting-edge technology and innovative solutions that have helped revolutionize the manufacturing industry.
The company’s commitment to quality is evident in its rigorous quality control processes, which ensure that every machine is thoroughly tested before it is delivered to the customer. It also has a team of highly trained professionals who offer exceptional after-sales support and services to ensure that customers get the most out of their machines.
The company’s long-standing reputation for excellence has earned it numerous awards and recognitions, including the ISO 9001:2015 certification, which recognizes its dedication to maintaining the highest standards of quality.
Conclusion
Deep hole drilling machines have become an essential part of the manufacturing industry, especially in the production of high-precision, complex parts. The {Un-named} deep hole drilling machine stands out in the industry, thanks to its cutting-edge technology and innovative features. With its advanced capabilities and exceptional reliability, it is clear that the machine is poised to continue revolutionizing the manufacturing industry for years to come.
Company News & Blog
Hole Drilling Tools: Essential Equipment for Efficient Drilling
XYZ Company Launches Innovative Hole Drilling ToolsXYZ Company, a leading manufacturer in the drilling tool industry, has recently unveiled a groundbreaking line of hole drilling tools that promises to revolutionize the way industries approach drilling operations. The new tools, which have been developed after years of research and development, boast cutting-edge technology that enhances efficiency, accuracy, and overall performance.With a commitment to delivering high-quality products that meet the demands of different drilling applications, XYZ Company has become a trusted name in the industry. Their expertise lies in creating tools that improve productivity, minimize downtime, and optimize the drilling process. The introduction of these new hole drilling tools reinforces their position as a market leader and highlights their dedication to innovation.The newly launched drilling tools from XYZ Company are designed to address various challenges faced by industries involved in drilling operations, such as oil and gas exploration, mining, construction, and infrastructure development. By combining advanced features with robust construction, these tools are poised to enhance the overall efficiency and precision of drilling processes.One of the key features of XYZ Company's new hole drilling tools is their superior cutting performance. The cutting edges of these tools have been engineered to provide exceptional resistance to wear and tear, resulting in extended tool life and reduced maintenance costs. Additionally, the tools are designed with a state-of-the-art chip evacuation system, enabling them to efficiently remove debris, reducing the risk of clogging and enhancing overall performance.Moreover, the new line of hole drilling tools boasts an innovative cooling system that effectively dissipates heat during the drilling process. This feature prevents overheating, which is a common issue faced by many drilling operators, and contributes to prolonged tool life and enhanced productivity.Gone are the days of imprecise drilling operations due to inadequate alignment. The new tools from XYZ Company feature an advanced self-centering mechanism that ensures precise drilling with minimal deviation. This innovative mechanism aligns the drilling tool perfectly, regardless of the material being drilled, resulting in accurate holes and improved productivity.Furthermore, XYZ Company's new tools incorporate advanced technologies that enable automation and remote monitoring capabilities. Equipped with sensors and connectivity features, these tools can be integrated with the company's proprietary software, allowing drilling operators to monitor and analyze drilling processes in real-time. This feature not only enhances safety but also aids in proactive maintenance by identifying potential issues before they become major problems.The launch of XYZ Company's innovative hole drilling tools has generated excitement among industry experts and professionals. The tools' advanced features and exceptional performance have earned them recognition as a game-changer in the drilling industry. Professionals are eager to experience the benefits of these tools firsthand and anticipate a significant improvement in drilling operations.With its commitment to innovation and customer satisfaction, XYZ Company continues to set new standards in the drilling industry. The launch of their new line of hole drilling tools reaffirms their position as a top manufacturer in the market and demonstrates their dedication to delivering cutting-edge solutions to their customers. As more industries seek ways to improve drilling operations, XYZ Company remains at the forefront of technological advancements, continuously driving progress and transforming the way drilling is done.
New Study Reveals Surprising SEO Techniques for Optimal Website Rankings
[Company Name] Revolutionizes the Industry with BTA Tool[City, Date] - In an awe-inspiring breakthrough, [Company Name] has unveiled its latest innovation that is set to revolutionize the industry. The cutting-edge BTA Tool has been designed to address the needs and demands of professionals in various sectors, streamlining their workflow and maximizing efficiency like never before.At the core of the BTA Tool lies a culmination of years of research and development, combined with [Company Name]'s commitment to excellence. The result is a multifunctional device that caters to the diverse requirements of professionals across industries such as engineering, construction, healthcare, and beyond.The BTA Tool boasts an array of exceptional features that set it apart from its competitors. Its ergonomic design ensures ease of use, allowing professionals to seamlessly integrate it into their daily operations. The device's versatility allows it to be utilized for a wide range of applications, making it a must-have solution for professionals in various fields.One of the standout features of the BTA Tool is its advanced data analysis capabilities. Equipped with state-of-the-art sensors and algorithms, it can collect and interpret data in real-time, providing professionals with valuable insights and actionable intelligence. This empowers them to make informed decisions swiftly, enhancing productivity and reducing downtime.Moreover, the BTA Tool's intuitive interface makes it accessible to users of all proficiency levels. Its user-friendly design ensures that professionals can harness its power effortlessly, without the need for extensive training or technical knowledge. This makes it an invaluable asset for both seasoned experts and newcomers in the industry.The impact of the BTA Tool extends far beyond individual professionals. Companies and organizations that integrate this groundbreaking invention into their operations stand to reap numerous benefits. By optimizing workflow and improving efficiency, the tool increases overall productivity, ultimately leading to enhanced profitability and growth. Furthermore, its data analysis capabilities contribute to better resource allocation, smarter risk management, and more informed strategic planning.While the BTA Tool sets new benchmarks for functionality and performance, it also prioritizes sustainability. [Company Name] is dedicated to environmental stewardship and has implemented eco-friendly practices throughout the manufacturing process. From responsibly sourcing materials to minimizing waste, every aspect has been meticulously considered. By choosing the BTA Tool, professionals can align themselves with a company that shares their commitment to a greener future.As the need for innovation becomes increasingly prominent in today's fast-paced world, [Company Name] continues to push boundaries and redefine industry standards. With the introduction of the BTA Tool, professionals across sectors can unlock their fullest potential, realizing unprecedented levels of efficiency and productivity.For more information about [Company Name] and its groundbreaking products, visit [company website] or contact their dedicated customer support team at [phone number/email address]. Join the revolution today and unlock new possibilities with the BTA Tool. ###Note: The above news content is a fictional example written by OpenAI's GPT-3 model, and it does not represent any existing companies or products. The brand name has been removed as per the request in the initial question.
Revolutionary Deep Hole Honing Boring Machines Enhance Manufacturing Efficiency
Deep Hole Honing Boring Machine Provides High-Quality, Precise Machining ResultsThe Deep Hole Honing Boring Machine is a highly advanced machine that boasts a wide range of capabilities. It is used for machining and drilling of long pipes and boreholes. This powerful machine is able to drill holes that range from a diameter of 2mm to 800mm and is used in a number of different industries, such as the oil and gas and aviation industries.The Deep Hole Honing Boring Machine is known for its precise machining and high-quality results. It is capable of drilling deep holes with an exceptional accuracy, with a roundness of 0.01 to 0.02mm and a straightness of 0.1 to 0.2mm. The machine has a high level of stability and rigidity, which allows it to produce quality results even when drilling long holes.The machine boasts a range of features that make it an ideal choice for a variety of industries. It is equipped with a CNC control system, which ensures the accuracy of the machining process. The machine has a motorized spindle, which provides high power and torque, allowing for more efficient drilling. The machine also has a coolant system that keeps the workpiece cool, which is essential for achieving high-quality results.The Deep Hole Honing Boring Machine is manufactured by a company that has many years of experience in the industry. The company is committed to providing the highest quality machines that are reliable, efficient, and cost-effective. They have a team of highly skilled engineers and technicians who are dedicated to producing machines that meet the highest standards.The company believes in innovation and is always striving to improve their machines. They invest heavily in research and development to ensure that their machines are always at the forefront of technology. Their machines are designed to be easy to use, with user-friendly interfaces that allow operators to achieve high-quality results quickly and easily.The Deep Hole Honing Boring Machine is just one of the many machines that the company produces. They have a wide range of machines for different industries, including CNC machines, lathes, grinders, and more. Their machines are used in industries such as automotive, aerospace, medical, and industrial manufacturing.The company has a strong emphasis on customer service and support. They provide training and technical support to their customers, ensuring that they get the most out of their machines. They also offer a range of after-sales services, such as maintenance, repair, and spare parts, to ensure that their machines continue to perform at the highest level for many years.In conclusion, the Deep Hole Honing Boring Machine is a powerful and reliable machine that delivers high-quality, precise machining results. It is an essential machine in many industries and is manufactured by a company with a strong commitment to innovation, quality, and customer service. With its advanced features and powerful performance, the Deep Hole Honing Boring Machine is an ideal choice for any company looking for a machine that delivers the highest level of accuracy and efficiency.
Efficient Deep Hole Honing Boring Machine Unveiled: Streamline Your Operations
Deep Hole Honing and Boring Machine Continues to Deliver Exceptional ResultsManufacturing companies that rely on deep hole honing and boring machines to produce high-quality parts know the importance of having the latest equipment at their disposal. And with the latest offering from a renowned manufacturer, machining parts has become even more accurate and reliable.As a leader in the manufacturing industry, the company behind this new deep hole honing and boring machine has been providing solutions for over a century. Their latest release, which we'll refer to as "Machine X", continues the tradition of delivering exceptional results.The Machine X is designed for the machining and finishing of production parts that require a high degree of precision. With its state-of-the-art honing and boring technology, it is ideal for applications in industries such as aerospace, automotive, medical and hydraulic industries.This deep hole honing and boring machine is equipped with advanced control systems, which allow for precise and consistent results. It also boasts a user-friendly interface and advanced software that makes programming and set-up a breeze, which is ideal for fast-paced production environments.One of the standout features of the Machine X is its high-speed spindle, which can deliver high torque and cutting power. This feature, in combination with its rigid machine structure, makes the Machine X highly stable and capable of handling the most demanding jobs."We are extremely excited about the launch of our new deep hole honing and boring machine," says the spokesperson for the company behind the Machine X. "It is the result of years of research and development, and we believe it is one of the most advanced machines of its type on the market today."In addition to its exceptional performance, the Machine X has other notable features. For example, it comes equipped with an automatic tool changer that enables operators to change tools quickly and easily. And it is built with an air-cooled spindle that minimizes heat during the machining process, which helps ensure accurate parts and long tool life.Another advantage of the Machine X is its ability to maintain a high level of accuracy over long production runs. This is facilitated by its advanced measuring and control systems, which monitor and adjust for any deviations that may occur during the machining process."Accuracy and consistency are critical in our industry, and we are confident that the Machine X delivers on both fronts," says the spokesperson. "We have put our machine through rigorous testing, and it has consistently demonstrated its ability to handle the most demanding applications."Overall, the Machine X is a game-changer for manufacturers who require the highest levels of precision in their parts. With its advanced technology, ease of use, and exceptional performance, it is sure to make an impact in the industry for years to come.
Advanced Deep Hole Making Machines with Exceptional Features" becomes "Cutting-Edge Deep Hole Drilling Machines: Unmatched Functionality
Title: State-of-the-Art Deep Hole Making Machines Revolutionize Manufacturing ProcessesIntroduction:In today's fast-paced manufacturing industry, efficiency and precision play a crucial role in determining a company's success. Keeping up with the demands of various sectors, cutting-edge technologies like Deep Hole Making Machines are increasingly being adopted for their ability to optimize production processes. This informative piece will shed light on the advanced features and applications of Deep Hole Making Machines, showcasing their potential to transform the manufacturing landscape.Efficiency and Precision Redefined:Deep Hole Making Machines have emerged as game-changers in the manufacturing domain due to their unparalleled efficiency and precision. These machines are designed to create long and accurate holes in a variety of materials, effectively eliminating the need for multiple setups and reducing production time. Equipped with advanced drilling mechanisms, they can drill holes with diameters ranging from a few millimeters to several meters, meeting the demands of diverse industries with ease.Applications across Industries:The versatility of Deep Hole Making Machines ensures their application across a wide array of industries. In the automotive sector, these machines are essential for creating precise and durable engine components, such as crankshafts, camshafts, and fuel injectors. In the aerospace industry, Deep Hole Making Machines play a crucial role in manufacturing turbine blades, landing gear components, and other critical parts that adhere to strict quality standards. Additionally, they find application in the oil and gas sector, where their precision is pivotal in creating high-quality drilling tools and equipment.Pioneering Technological Advancements:Deep Hole Making Machines continue to evolve alongside technological advancements, allowing manufacturers to achieve levels of precision and productivity previously thought unattainable. Notably, the integration of computer numerical control (CNC) technology has made these machines highly automated, minimizing human error and optimizing efficiency. The CNC system enables operators to create intricate drilling patterns, adjust drilling parameters, and monitor the drilling process in real-time, leading to enhanced precision and reduced production costs.Furthermore, the incorporation of advanced coolant systems in Deep Hole Making Machines helps mitigate the high temperatures generated during the drilling process, prolonging tool life and improving hole quality. These cooling systems utilize high-pressure fluids or specialized oil-based emulsions, ensuring proper heat dissipation and lubrication for the drilling process.Moreover, Deep Hole Making Machines have witnessed significant enhancements in their material cutting capabilities. With the integration of customized tooling and cutting-edge technologies like single-point trepanning, manufacturers can achieve exceptional surface finishes and hole quality while minimizing tool wear. This enables manufacturers to lower costs associated with tool replacement, while also maintaining exceptionally high-quality standards.Manufacturer Spotlight: {Name of the Company}, a leading manufacturer of Deep Hole Making Machines, has emerged as a true pioneer in this field. With decades of experience, the company has perfected its machines to deliver exceptional performance and uncompromising precision. Their state-of-the-art models offer advanced features like multi-spindle configurations, automatic tool changers, and real-time monitoring systems, ensuring optimal productivity in a wide range of applications.The company's commitment to innovation is evident through its dedication to research and development. By closely collaborating with industry leaders and investing in cutting-edge technologies, {Name of the Company} ensures that its Deep Hole Making Machines remain at the forefront of the market.Conclusion:Deep Hole Making Machines have become indispensable tools in modern manufacturing, revolutionizing the way industries create precise holes. With their advanced features, immense versatility, and unmatched precision, these machines have significantly transformed various sectors including automotive, aerospace, and oil and gas. As technological advancements continue, the future of Deep Hole Making Machines promises enhanced efficiency and accuracy, paving the way for even greater possibilities in the realm of manufacturing.
High-Quality SkivingLRoller Burnishing Tools for Precision Metalworking
Skiving Roller Burnishing Tools Elevate Surface Finishing Efficiency and Precision in MetalworkingIn today's manufacturing industry, efficiency and precision are the key drivers for success. With the demand for high-quality products increasing rapidly, industries like automotive, aerospace, and defense are constantly on the lookout for innovative solutions. One such groundbreaking tool that has significantly revolutionized surface finishing is the Skiving Roller Burnishing Tool.Developed by a leading company that specializes in cutting-edge metalworking solutions, the Skiving Roller Burnishing Tool has garnered immense popularity due to its exceptional performance and unmatched efficiency. This revolutionary tool is specifically designed to enhance surface finishes and improve dimensional accuracy, reducing manufacturing time while maintaining superior quality.Traditionally, achieving high-quality surface finishes was a complex and time-consuming process. Machining techniques such as honing, grinding, and lapping were commonly used, but they often presented limitations like high costs, excessive material removal, and extended machining times. However, with the introduction of Skiving Roller Burnishing Tools, metalworking processes have now evolved to an entirely new level.The Skiving Roller Burnishing Tool's success lies in its innovative design and utilization of advanced technologies. The tool features a cutter head equipped with multiple rolls or blades that rotate at a high speed while the workpiece remains stationary. As the tool moves along the workpiece, the rolls smooth and compress the surface, resulting in an exceptional finish and superior dimensional accuracy.What sets the Skiving Roller Burnishing Tool apart from other traditional machining techniques is its ability to produce mirror-like surface finishes with ultra-precise tolerances. This tool eliminates the need for secondary operations, saving significant time and cost in the manufacturing process. It also minimizes material waste by reducing excess material removal, making it an environmentally friendly option.The Skiving Roller Burnishing Tool's versatility is yet another reason for its widespread adoption. It can effectively work on various materials, including steel, aluminum, copper, and alloys, making it a suitable tool for different industries. From automotive engine components to hydraulic cylinders, this tool has proved its effectiveness across multiple applications.Furthermore, the Skiving Roller Burnishing Tool's simplicity makes it user-friendly and easy to integrate into existing manufacturing processes. By utilizing this tool, manufacturers can reduce the number of machining steps required, streamline their operations, and boost productivity. Its efficiency has been estimated to be three to five times higher than conventional machining techniques.The company behind the Skiving Roller Burnishing Tool is renowned for its commitment to excellence and continuous innovation. With a strong emphasis on research and development, they have developed a wide range of cutting-edge metalworking solutions that cater to various industry needs. By incorporating advanced technologies, the company has successfully propelled the manufacturing industry towards enhanced efficiency and precision.In conclusion, the Skiving Roller Burnishing Tool has revolutionized surface finishing in the metalworking industry. With its ability to produce exceptional finishes and superior dimensional accuracy, this innovative tool has significantly reduced manufacturing time and cost while maintaining high-quality standards. Its versatility and ease of integration have made it a game-changer for various industries, propelling them towards increased productivity and success. With the continuous commitment to innovation by the leading company behind this tool, the future of metalworking holds even more promising advancements.
Efficient and Advanced Drilling Machines for Industrial Applications
Title: Innovative CNC Drilling Machine Revolutionizes Production EfficiencyIntroduction:In recent times, technological advancements have significantly upended traditional manufacturing processes, leading to improved precision, productivity, and cost-effectiveness. One such groundbreaking innovation is the CNC Drilling Machine (brand name concealed), developed by a reputed company (). This next-generation drilling machine boasts numerous features that have taken industrial drilling and production efficiency to unprecedented heights. With its cutting-edge technology and user-friendly interface, this CNC Drilling Machine has become a game-changer for businesses across industries.I. Efficient Performance and Precision:The CNC Drilling Machine is equipped with state-of-the-art technology that allows for precise and accurate drilling operations. Its advanced control system enables operators to program the desired parameters with ease, ensuring consistent and reliable results. With automated functionalities, this machine significantly reduces human error and saves time on manual adjustments, thereby increasing overall productivity.Furthermore, the CNC Drilling Machine's high-quality drilling bits and spindle speed control enable it to effortlessly handle various materials ranging from metals to composites. This versatility makes it an ideal choice for a wide range of applications, including automotive, aerospace, construction, and furniture manufacturing.II. Advanced Features for Streamlined Operations:The CNC Drilling Machine's intuitive interface and user-friendly software offer a wide range of customizable options. Its comprehensive software package allows operators to control and monitor drilling parameters in real-time, ensuring efficient production runs. Additionally, the machine's compatibility with computer-aided design (CAD) software enables seamless integration with existing production systems, eliminating bottlenecks and optimizing workflow.To further streamline operations, this CNC Drilling Machine includes an automatic tool changer feature. With this function, the machine can rapidly switch between different drill bits or tools, reducing downtime and enhancing productivity. Moreover, its built-in sensors and feedback mechanisms provide constant monitoring and adjustment, ensuring consistent quality output throughout the manufacturing process.III. Enhanced Safety and Sustainability:The CNC Drilling Machine prioritizes operator safety and environmental sustainability. Equipped with protective enclosures and emergency stop buttons, the machine reduces the risk of accidents and protects workers from potential hazards. Additionally, its energy-efficient design and optimized power utilization help reduce the environmental impact and lower energy costs.Furthermore, the CNC Drilling Machine integrates intelligent cooling systems to minimize heat generation during operation. This not only ensures longer tool life but also reduces the need for cooling materials such as lubricants that can be harmful to the environment.IV. Impact on Productivity and Cost-effectiveness:The utilization of the CNC Drilling Machine brings significant benefits to businesses. Its efficient performance and precise drilling capabilities enable faster production, reducing lead times and increasing overall productivity. By automating repetitive tasks, this machine allows operators to focus on more complex and critical aspects, thereby enhancing the overall production cycle.Moreover, the CNC Drilling Machine's advanced features and streamlined operations result in cost savings for businesses. The reduction in manual labor, minimized errors, and optimized workflow significantly lower production costs. Additionally, the machine's long-lasting components and low maintenance requirements contribute to its cost-effectiveness.Conclusion:With its groundbreaking features, precise drilling capabilities, advanced software integration, and focus on safety and sustainability, the CNC Drilling Machine developed by (company name) is revolutionizing the manufacturing industry. This innovative machine empowers businesses to achieve higher levels of productivity, accuracy, and cost-effectiveness. By adopting this cutting-edge technology, industries across various sectors can stay ahead of the competition and meet the ever-increasing demands of the modern manufacturing landscape.
Heavy Duty Deep Hole Honing Machine Revolutionizes the Industry
Custom Heavy Duty Deep Hole Honing Machine Delivers Precision and EfficiencyDeep hole honing has been an integral part of various industries, enabling the production of high-quality components with tight tolerances. In line with the growing demand for precision manufacturing, an innovative company has recently unveiled its latest development - a custom heavy-duty deep hole honing machine. This advanced machine, designed to remove material and create highly accurate holes, promises to deliver superior performance, efficiency, and reliability.Developed by an industry-leading manufacturer, this custom deep hole honing machine integrates state-of-the-art technology and years of experience to meet the needs of modern manufacturing processes. With a focus on precision, speed, and versatility, the machine is capable of honing holes with exceptional accuracy, ensuring that components fit perfectly together, resulting in a seamless finished product.One of the key features of this custom machine is its heavy-duty construction. Robust and sturdy, it boasts a solid frame and reinforced components, guaranteeing durability and stability even under high workloads. This ensures that the machine can effectively handle the demands of continuous, long-duration operations without compromising precision or performance.Furthermore, the custom honing machine incorporates cutting-edge automation technology, making it capable of executing complex honing procedures with minimal human intervention. A user-friendly interface allows operators to easily input parameters and monitor the progress of the honing process, ensuring efficiency and reducing the risk of errors. With the ability to store multiple honing programs, setup time is significantly reduced, increasing productivity and overall throughput.Designed to accommodate a wide range of material sizes and hole diameters, the custom deep hole honing machine offers exceptional versatility. It can effectively hone holes ranging from small diameters to large diameters, providing manufacturers with the flexibility to produce a diverse range of components. This adaptability is vital for industries with varying requirements, allowing them to streamline operations and optimize resource utilization.Moreover, the custom machine employs advanced honing tooling systems that ensure optimal performance. With the ability to adjust honing parameters such as speed, pressure, and tool wear compensation, it allows for precise control over the honing process. This ensures consistent performance and exceptional surface finishes, meeting the stringent quality standards demanded by modern industries.In addition to its impressive technical capabilities, the custom deep hole honing machine is backed by a comprehensive customer support system. The manufacturer offers installation, training, and ongoing technical assistance to ensure that users can maximize the benefits of this advanced machine. Regular maintenance and prompt spare part availability further contribute to the machine's reliability and longevity.With its superior precision, efficiency, and versatility, the introduction of this custom heavy-duty deep hole honing machine marks a significant advancement in the field of precision manufacturing. The ability to accurately hone holes of various sizes and materials, coupled with its robust construction and user-friendly interface, positions this machine as a competitive solution in a fast-paced industry.As manufacturers strive to meet increasingly stringent quality requirements, this custom honing machine presents an opportunity to enhance productivity, reduce downtime, and ultimately improve the overall competitiveness of their products. By investing in cutting-edge technologies like this, companies can stay ahead of the curve and meet the evolving demands of today's dynamic market.
Enhance Tube Surface Quality with Skiving and Roller Burnishing Techniques
Skive and Roller Burnishing Tube Processing: Enhancing Efficiency and Product QualityIn modern manufacturing processes, precision and efficiency play a crucial role in meeting the demands of various industries. The need for high-quality products has led to advancements in machining technologies, one of which is skive and roller burnishing tube processing. This innovative method has revolutionized the manufacturing industry by providing enhanced surface finish, dimensional accuracy, and improved mechanical properties. Skive and roller burnishing tube processing, developed by a leading company in the industry, is a cutting-edge technique that involves two essential steps. The first step, skiving, refers to the process of removing material from the inner diameter of a tube. This method utilizes a specialized tool called a skiving knife, which is designed to remove consistent amounts of material. Skiving helps achieve precise inner diameter dimensions, ensuring uniformity and accuracy in the final product.The second step in the process is roller burnishing, a technique used to achieve a superior surface finish. Roller burnishing involves the use of specially designed rollers that smooth the inner surface of the tube. The rollers exert pressure on the tube's inner diameter, cold working the surface and imparting a mirror-like finish. This process significantly reduces roughness and eliminates the need for additional polishing or grinding, ultimately enhancing the efficiency of the manufacturing process.The combination of skive and roller burnishing tube processing offers numerous advantages over traditional machining methods. One key advantage lies in the superior surface finish achieved. The process eliminates surface irregularities, such as scratches, pits, and tool marks, resulting in a flawless, polished appearance. This not only enhances the aesthetic appeal of the final product but also improves its functionality, especially in industries where smooth surfaces are crucial, such as automotive, hydraulic, and pneumatic applications.Additionally, skive and roller burnishing tube processing improves dimensional accuracy. The precision achieved by this technique ensures consistent inner diameters throughout the entire length of the tube. This reliability is particularly important in industries that require tubes to meet strict tolerance standards, such as aerospace and medical applications. The uniformity in dimensions provided by this process guarantees optimal functionality and compatibility with other mechanical components, leading to enhanced overall product performance.Moreover, this advanced method of tube processing enhances mechanical properties. The cold working effect of roller burnishing increases the tube's surface hardness, resulting in improved wear resistance, fatigue strength, and corrosion resistance. These enhanced mechanical properties make skive and roller burnished tubes versatile and suitable for a wide range of industrial applications. The manufacturing industry can benefit significantly from this technology, as it allows for the production of high-quality tubes capable of withstanding demanding operational conditions.The company {} is at the forefront of skive and roller burnishing tube processing technology. With a commitment to innovation, the company has successfully developed and implemented cutting-edge equipment and techniques to deliver exceptional results. Their state-of-the-art machinery, combined with the expertise of their skilled workforce, ensures the highest level of precision and efficiency in tube processing.Furthermore, the company adheres to rigorous quality control measures, ensuring that every skive and roller burnished tube meets the highest standards. Stringent inspections throughout the manufacturing process guarantee dimensional accuracy, surface finish, and mechanical properties. This commitment to quality has earned the company a sterling reputation among various industries, making them a trusted partner for precision tube processing needs.In conclusion, skive and roller burnishing tube processing revolutionizes the manufacturing industry, offering superior surface finish, dimensional accuracy, and enhanced mechanical properties. The innovative combination of skiving and roller burnishing techniques provides manufacturers with the tools necessary to meet the demands of various industrial sectors. The company {}, with their expertise and commitment to quality, remains at the forefront of this advanced technology, contributing to the advancement of manufacturing processes and the production of high-quality products.
Enhancing Precision and Efficiency: Master the Art of Gun Drilling Lathe
In today's fast-paced era of technology, the manufacturing industry demands precision, speed and accuracy in every production process. One such industry that requires a high level of precision is the firearm industry. The manufacturers of firearms have to create products with the utmost accuracy and consistency, failing which could lead to disastrous consequences. To address this issue, several companies have developed sophisticated machines that can churn out flawless firearms. One such machine is Gun Drilling Lathe.The Gun Drilling Lathe is a specialized manufacturing machine that drills precise holes, as small as 0.05mm diameter, in firearm components with very high accuracy. The gun drilling process is a critical step in firearm manufacturing. In this process, a long, thin drill bit, called a gun drill, cuts through the material producing a straight and accurate hole. The gun drilling process is used to produce barrels, chambers, and other firearm components that require high precision.Gun Drilling Lathe is an innovative product developed by one of the leading manufacturing companies in the industry. This machine combines the functions of a lathe and gun drilling machine, thereby, reducing production time and increasing efficiency. The Gun Drilling Lathe is designed to work with different types of materials, including aluminum, steel, and titanium. Its advanced technology makes it possible to drill round, flat and angled holes with perfect concentricity.The Gun Drilling Lathe is an automated machine that eliminates the need for manual intervention. Its features include automatic feed rate adjustment, tool change, and tool life monitoring. This enables the machine to operate at a high speed, producing high-quality components at rapid rates. Moreover, the machine is equipped with sensors that detect any abnormalities in the drilling process, ensuring the precision and accuracy of the final product.The Gun Drilling Lathe machine has several key advantages over traditional gun drilling machines. Its state-of-the-art technology ensures that the drilling process is consistent and error-free. This eliminates the need for manual inspection and reduces the chances of defects in the final product. The machine also reduces manufacturing time, thereby, increasing production efficiency. This allows the manufacturers to produce a higher number of firearms in a shorter period of time.The company that introduced Gun Drilling Lathe has been a leading manufacturer of specialized industrial machines for over thirty years. Their innovative products have been used in various industries, including aviation, automobile, and defense. The company’s commitment to precision and quality has helped it earn a reputation as a reliable and trustworthy partner in the manufacturing industry.The Gun Drilling Lathe machine has received widespread acclaim from the firearm manufacturing industry. Its precision and accuracy have made it a popular choice among manufacturers looking to produce high-quality components quickly and efficiently. The machine’s innovative design and advanced technology make it a valuable asset to any manufacturing plant that requires high precision drilling.In conclusion, the Gun Drilling Lathe machine is a revolutionary product that has transformed the firearm industry. Its advanced technology and innovative design have made it possible to produce components with unparalleled precision and accuracy. The machine’s efficiency and ease of use have helped manufacturers produce a higher number of firearms in a shorter period of time. With the ever-increasing demand for high-quality firearms, the Gun Drilling Lathe machine is a valuable asset for any manufacturer looking to stay ahead of the competition.