Heavy Duty Deep Hole Honing Machine Revolutionizes the Industry
By:Admin
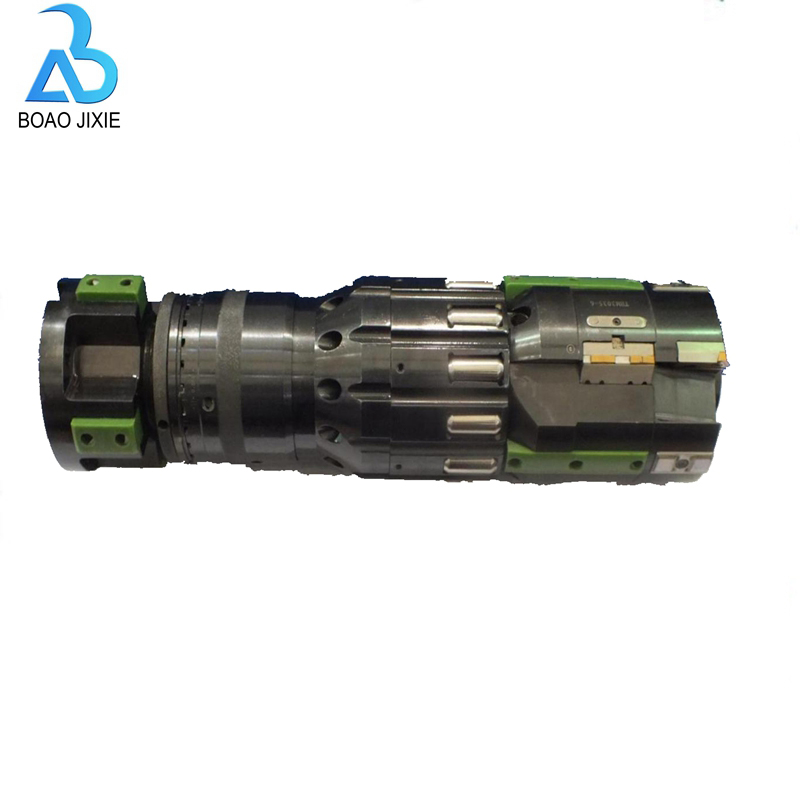
Deep hole honing has been an integral part of various industries, enabling the production of high-quality components with tight tolerances. In line with the growing demand for precision manufacturing, an innovative company has recently unveiled its latest development - a custom heavy-duty deep hole honing machine. This advanced machine, designed to remove material and create highly accurate holes, promises to deliver superior performance, efficiency, and reliability.
Developed by an industry-leading manufacturer, this custom deep hole honing machine integrates state-of-the-art technology and years of experience to meet the needs of modern manufacturing processes. With a focus on precision, speed, and versatility, the machine is capable of honing holes with exceptional accuracy, ensuring that components fit perfectly together, resulting in a seamless finished product.
One of the key features of this custom machine is its heavy-duty construction. Robust and sturdy, it boasts a solid frame and reinforced components, guaranteeing durability and stability even under high workloads. This ensures that the machine can effectively handle the demands of continuous, long-duration operations without compromising precision or performance.
Furthermore, the custom honing machine incorporates cutting-edge automation technology, making it capable of executing complex honing procedures with minimal human intervention. A user-friendly interface allows operators to easily input parameters and monitor the progress of the honing process, ensuring efficiency and reducing the risk of errors. With the ability to store multiple honing programs, setup time is significantly reduced, increasing productivity and overall throughput.
Designed to accommodate a wide range of material sizes and hole diameters, the custom deep hole honing machine offers exceptional versatility. It can effectively hone holes ranging from small diameters to large diameters, providing manufacturers with the flexibility to produce a diverse range of components. This adaptability is vital for industries with varying requirements, allowing them to streamline operations and optimize resource utilization.
Moreover, the custom machine employs advanced honing tooling systems that ensure optimal performance. With the ability to adjust honing parameters such as speed, pressure, and tool wear compensation, it allows for precise control over the honing process. This ensures consistent performance and exceptional surface finishes, meeting the stringent quality standards demanded by modern industries.
In addition to its impressive technical capabilities, the custom deep hole honing machine is backed by a comprehensive customer support system. The manufacturer offers installation, training, and ongoing technical assistance to ensure that users can maximize the benefits of this advanced machine. Regular maintenance and prompt spare part availability further contribute to the machine's reliability and longevity.
With its superior precision, efficiency, and versatility, the introduction of this custom heavy-duty deep hole honing machine marks a significant advancement in the field of precision manufacturing. The ability to accurately hone holes of various sizes and materials, coupled with its robust construction and user-friendly interface, positions this machine as a competitive solution in a fast-paced industry.
As manufacturers strive to meet increasingly stringent quality requirements, this custom honing machine presents an opportunity to enhance productivity, reduce downtime, and ultimately improve the overall competitiveness of their products. By investing in cutting-edge technologies like this, companies can stay ahead of the curve and meet the evolving demands of today's dynamic market.
Company News & Blog
Hole Drilling Tools: Essential Equipment for Efficient Drilling
XYZ Company Launches Innovative Hole Drilling ToolsXYZ Company, a leading manufacturer in the drilling tool industry, has recently unveiled a groundbreaking line of hole drilling tools that promises to revolutionize the way industries approach drilling operations. The new tools, which have been developed after years of research and development, boast cutting-edge technology that enhances efficiency, accuracy, and overall performance.With a commitment to delivering high-quality products that meet the demands of different drilling applications, XYZ Company has become a trusted name in the industry. Their expertise lies in creating tools that improve productivity, minimize downtime, and optimize the drilling process. The introduction of these new hole drilling tools reinforces their position as a market leader and highlights their dedication to innovation.The newly launched drilling tools from XYZ Company are designed to address various challenges faced by industries involved in drilling operations, such as oil and gas exploration, mining, construction, and infrastructure development. By combining advanced features with robust construction, these tools are poised to enhance the overall efficiency and precision of drilling processes.One of the key features of XYZ Company's new hole drilling tools is their superior cutting performance. The cutting edges of these tools have been engineered to provide exceptional resistance to wear and tear, resulting in extended tool life and reduced maintenance costs. Additionally, the tools are designed with a state-of-the-art chip evacuation system, enabling them to efficiently remove debris, reducing the risk of clogging and enhancing overall performance.Moreover, the new line of hole drilling tools boasts an innovative cooling system that effectively dissipates heat during the drilling process. This feature prevents overheating, which is a common issue faced by many drilling operators, and contributes to prolonged tool life and enhanced productivity.Gone are the days of imprecise drilling operations due to inadequate alignment. The new tools from XYZ Company feature an advanced self-centering mechanism that ensures precise drilling with minimal deviation. This innovative mechanism aligns the drilling tool perfectly, regardless of the material being drilled, resulting in accurate holes and improved productivity.Furthermore, XYZ Company's new tools incorporate advanced technologies that enable automation and remote monitoring capabilities. Equipped with sensors and connectivity features, these tools can be integrated with the company's proprietary software, allowing drilling operators to monitor and analyze drilling processes in real-time. This feature not only enhances safety but also aids in proactive maintenance by identifying potential issues before they become major problems.The launch of XYZ Company's innovative hole drilling tools has generated excitement among industry experts and professionals. The tools' advanced features and exceptional performance have earned them recognition as a game-changer in the drilling industry. Professionals are eager to experience the benefits of these tools firsthand and anticipate a significant improvement in drilling operations.With its commitment to innovation and customer satisfaction, XYZ Company continues to set new standards in the drilling industry. The launch of their new line of hole drilling tools reaffirms their position as a top manufacturer in the market and demonstrates their dedication to delivering cutting-edge solutions to their customers. As more industries seek ways to improve drilling operations, XYZ Company remains at the forefront of technological advancements, continuously driving progress and transforming the way drilling is done.
Heavy Duty Deep Hole Honing Machine Revolutionizes the Industry
Custom Heavy Duty Deep Hole Honing Machine Delivers Precision and EfficiencyDeep hole honing has been an integral part of various industries, enabling the production of high-quality components with tight tolerances. In line with the growing demand for precision manufacturing, an innovative company has recently unveiled its latest development - a custom heavy-duty deep hole honing machine. This advanced machine, designed to remove material and create highly accurate holes, promises to deliver superior performance, efficiency, and reliability.Developed by an industry-leading manufacturer, this custom deep hole honing machine integrates state-of-the-art technology and years of experience to meet the needs of modern manufacturing processes. With a focus on precision, speed, and versatility, the machine is capable of honing holes with exceptional accuracy, ensuring that components fit perfectly together, resulting in a seamless finished product.One of the key features of this custom machine is its heavy-duty construction. Robust and sturdy, it boasts a solid frame and reinforced components, guaranteeing durability and stability even under high workloads. This ensures that the machine can effectively handle the demands of continuous, long-duration operations without compromising precision or performance.Furthermore, the custom honing machine incorporates cutting-edge automation technology, making it capable of executing complex honing procedures with minimal human intervention. A user-friendly interface allows operators to easily input parameters and monitor the progress of the honing process, ensuring efficiency and reducing the risk of errors. With the ability to store multiple honing programs, setup time is significantly reduced, increasing productivity and overall throughput.Designed to accommodate a wide range of material sizes and hole diameters, the custom deep hole honing machine offers exceptional versatility. It can effectively hone holes ranging from small diameters to large diameters, providing manufacturers with the flexibility to produce a diverse range of components. This adaptability is vital for industries with varying requirements, allowing them to streamline operations and optimize resource utilization.Moreover, the custom machine employs advanced honing tooling systems that ensure optimal performance. With the ability to adjust honing parameters such as speed, pressure, and tool wear compensation, it allows for precise control over the honing process. This ensures consistent performance and exceptional surface finishes, meeting the stringent quality standards demanded by modern industries.In addition to its impressive technical capabilities, the custom deep hole honing machine is backed by a comprehensive customer support system. The manufacturer offers installation, training, and ongoing technical assistance to ensure that users can maximize the benefits of this advanced machine. Regular maintenance and prompt spare part availability further contribute to the machine's reliability and longevity.With its superior precision, efficiency, and versatility, the introduction of this custom heavy-duty deep hole honing machine marks a significant advancement in the field of precision manufacturing. The ability to accurately hone holes of various sizes and materials, coupled with its robust construction and user-friendly interface, positions this machine as a competitive solution in a fast-paced industry.As manufacturers strive to meet increasingly stringent quality requirements, this custom honing machine presents an opportunity to enhance productivity, reduce downtime, and ultimately improve the overall competitiveness of their products. By investing in cutting-edge technologies like this, companies can stay ahead of the curve and meet the evolving demands of today's dynamic market.
Revolutionary Deep Hole Honing Boring Machines Enhance Manufacturing Efficiency
Deep Hole Honing Boring Machine Provides High-Quality, Precise Machining ResultsThe Deep Hole Honing Boring Machine is a highly advanced machine that boasts a wide range of capabilities. It is used for machining and drilling of long pipes and boreholes. This powerful machine is able to drill holes that range from a diameter of 2mm to 800mm and is used in a number of different industries, such as the oil and gas and aviation industries.The Deep Hole Honing Boring Machine is known for its precise machining and high-quality results. It is capable of drilling deep holes with an exceptional accuracy, with a roundness of 0.01 to 0.02mm and a straightness of 0.1 to 0.2mm. The machine has a high level of stability and rigidity, which allows it to produce quality results even when drilling long holes.The machine boasts a range of features that make it an ideal choice for a variety of industries. It is equipped with a CNC control system, which ensures the accuracy of the machining process. The machine has a motorized spindle, which provides high power and torque, allowing for more efficient drilling. The machine also has a coolant system that keeps the workpiece cool, which is essential for achieving high-quality results.The Deep Hole Honing Boring Machine is manufactured by a company that has many years of experience in the industry. The company is committed to providing the highest quality machines that are reliable, efficient, and cost-effective. They have a team of highly skilled engineers and technicians who are dedicated to producing machines that meet the highest standards.The company believes in innovation and is always striving to improve their machines. They invest heavily in research and development to ensure that their machines are always at the forefront of technology. Their machines are designed to be easy to use, with user-friendly interfaces that allow operators to achieve high-quality results quickly and easily.The Deep Hole Honing Boring Machine is just one of the many machines that the company produces. They have a wide range of machines for different industries, including CNC machines, lathes, grinders, and more. Their machines are used in industries such as automotive, aerospace, medical, and industrial manufacturing.The company has a strong emphasis on customer service and support. They provide training and technical support to their customers, ensuring that they get the most out of their machines. They also offer a range of after-sales services, such as maintenance, repair, and spare parts, to ensure that their machines continue to perform at the highest level for many years.In conclusion, the Deep Hole Honing Boring Machine is a powerful and reliable machine that delivers high-quality, precise machining results. It is an essential machine in many industries and is manufactured by a company with a strong commitment to innovation, quality, and customer service. With its advanced features and powerful performance, the Deep Hole Honing Boring Machine is an ideal choice for any company looking for a machine that delivers the highest level of accuracy and efficiency.
Enhance Your Drilling Efficiency with the Innovative Double Spindle Drilling Machine
Double Spindle Drilling Machine Brings Unmatched Productivity and Efficiency to the Manufacturing IndustryRenowned for its innovative technological solutions, the leading manufacturing company introduces the latest addition to its product range: the Double Spindle Drilling Machine. The machine is tailor-made to help manufacturing companies enhance their productivity, accuracy, and efficiency while reducing costs. The Double Spindle Drilling Machine comes with industry-leading features, including a high-speed drilling capability, intelligent control system, and a robust structure designed for longevity and durability. The machine is versatile, making it easy for manufacturing companies of all sizes to streamline their drilling operations. The intelligent control system employed in the machine significantly enhances drilling precision while minimizing the risk of errors. With the automated system, the machine executes drilling processes with minimal involvement from human operators. This significantly reduces the workload on the operators and minimizes the possibility of errors from fatigue or other factors.In addition to precision, the machine boasts a high drilling speed that translates to unmatched productivity. The Double Spindle Drilling Machine executes drilling operations faster than older machines, accelerating the overall manufacturing process. Consequently, manufacturing companies can produce more goods in less time, increasing their revenue streams and profitability.The robust structure of the Double Spindle Drilling Machine renders it highly reliable and durable. The machine is made with top-quality materials that enhance its structural integrity, enabling it to withstand harsh manufacturing environments. This durability ensures that manufacturing companies can enjoy uninterrupted production processes, minimizing downtimes and maximizing operational efficiency.Moreover, the machine is designed with versatility in mind, making it easy to customize to suit the unique requirements of different manufacturing processes. The versatility of the machine makes it a cost-effective solution since manufacturing companies can repurpose it for other drilling operations instead of acquiring a new machine.According to the manufacturing company spokesperson, the Double Spindle Drilling Machine is expected to revolutionize the manufacturing industry, significantly streamlining drilling operations and enhancing productivity. The spokesperson added that the machine is designed for seamless integration with existing manufacturing processes, making the transition smooth and straightforward. The company's commitment to creating cutting-edge technological solutions dates back to its founding decades ago. Thanks to its unwavering commitment to innovation and customer satisfaction, the company has a proven track record of providing top-quality manufacturing machines that meet the unique needs of clients. Manufacturing companies that invest in the Double Spindle Drilling Machine can expect to enjoy a range of benefits, including increased productivity, reduced costs, enhanced accuracy, and improved drilling efficiency. The machine is designed to meet the highest quality standards while adhering to industry regulations and safety guidelines.In conclusion, the Double Spindle Drilling Machine is an excellent addition to the manufacturing industry, offering unmatched productivity and efficiency. The machine is designed for reliability, precision, speed, and durability, making it a cost-effective solution for manufacturing companies looking to streamline their drilling processes. With the machine, manufacturing companies can produce more goods in less time, reducing costs and increasing revenue streams. The innovative machine underscores the manufacturing company's unwavering commitment to creating top-quality technological solutions that solve real-world problems.
Advanced Deep Hole Making Machines with Exceptional Features" becomes "Cutting-Edge Deep Hole Drilling Machines: Unmatched Functionality
Title: State-of-the-Art Deep Hole Making Machines Revolutionize Manufacturing ProcessesIntroduction:In today's fast-paced manufacturing industry, efficiency and precision play a crucial role in determining a company's success. Keeping up with the demands of various sectors, cutting-edge technologies like Deep Hole Making Machines are increasingly being adopted for their ability to optimize production processes. This informative piece will shed light on the advanced features and applications of Deep Hole Making Machines, showcasing their potential to transform the manufacturing landscape.Efficiency and Precision Redefined:Deep Hole Making Machines have emerged as game-changers in the manufacturing domain due to their unparalleled efficiency and precision. These machines are designed to create long and accurate holes in a variety of materials, effectively eliminating the need for multiple setups and reducing production time. Equipped with advanced drilling mechanisms, they can drill holes with diameters ranging from a few millimeters to several meters, meeting the demands of diverse industries with ease.Applications across Industries:The versatility of Deep Hole Making Machines ensures their application across a wide array of industries. In the automotive sector, these machines are essential for creating precise and durable engine components, such as crankshafts, camshafts, and fuel injectors. In the aerospace industry, Deep Hole Making Machines play a crucial role in manufacturing turbine blades, landing gear components, and other critical parts that adhere to strict quality standards. Additionally, they find application in the oil and gas sector, where their precision is pivotal in creating high-quality drilling tools and equipment.Pioneering Technological Advancements:Deep Hole Making Machines continue to evolve alongside technological advancements, allowing manufacturers to achieve levels of precision and productivity previously thought unattainable. Notably, the integration of computer numerical control (CNC) technology has made these machines highly automated, minimizing human error and optimizing efficiency. The CNC system enables operators to create intricate drilling patterns, adjust drilling parameters, and monitor the drilling process in real-time, leading to enhanced precision and reduced production costs.Furthermore, the incorporation of advanced coolant systems in Deep Hole Making Machines helps mitigate the high temperatures generated during the drilling process, prolonging tool life and improving hole quality. These cooling systems utilize high-pressure fluids or specialized oil-based emulsions, ensuring proper heat dissipation and lubrication for the drilling process.Moreover, Deep Hole Making Machines have witnessed significant enhancements in their material cutting capabilities. With the integration of customized tooling and cutting-edge technologies like single-point trepanning, manufacturers can achieve exceptional surface finishes and hole quality while minimizing tool wear. This enables manufacturers to lower costs associated with tool replacement, while also maintaining exceptionally high-quality standards.Manufacturer Spotlight: {Name of the Company}, a leading manufacturer of Deep Hole Making Machines, has emerged as a true pioneer in this field. With decades of experience, the company has perfected its machines to deliver exceptional performance and uncompromising precision. Their state-of-the-art models offer advanced features like multi-spindle configurations, automatic tool changers, and real-time monitoring systems, ensuring optimal productivity in a wide range of applications.The company's commitment to innovation is evident through its dedication to research and development. By closely collaborating with industry leaders and investing in cutting-edge technologies, {Name of the Company} ensures that its Deep Hole Making Machines remain at the forefront of the market.Conclusion:Deep Hole Making Machines have become indispensable tools in modern manufacturing, revolutionizing the way industries create precise holes. With their advanced features, immense versatility, and unmatched precision, these machines have significantly transformed various sectors including automotive, aerospace, and oil and gas. As technological advancements continue, the future of Deep Hole Making Machines promises enhanced efficiency and accuracy, paving the way for even greater possibilities in the realm of manufacturing.
Enhance Tube Surface Quality with Skiving and Roller Burnishing Techniques
Skive and Roller Burnishing Tube Processing: Enhancing Efficiency and Product QualityIn modern manufacturing processes, precision and efficiency play a crucial role in meeting the demands of various industries. The need for high-quality products has led to advancements in machining technologies, one of which is skive and roller burnishing tube processing. This innovative method has revolutionized the manufacturing industry by providing enhanced surface finish, dimensional accuracy, and improved mechanical properties. Skive and roller burnishing tube processing, developed by a leading company in the industry, is a cutting-edge technique that involves two essential steps. The first step, skiving, refers to the process of removing material from the inner diameter of a tube. This method utilizes a specialized tool called a skiving knife, which is designed to remove consistent amounts of material. Skiving helps achieve precise inner diameter dimensions, ensuring uniformity and accuracy in the final product.The second step in the process is roller burnishing, a technique used to achieve a superior surface finish. Roller burnishing involves the use of specially designed rollers that smooth the inner surface of the tube. The rollers exert pressure on the tube's inner diameter, cold working the surface and imparting a mirror-like finish. This process significantly reduces roughness and eliminates the need for additional polishing or grinding, ultimately enhancing the efficiency of the manufacturing process.The combination of skive and roller burnishing tube processing offers numerous advantages over traditional machining methods. One key advantage lies in the superior surface finish achieved. The process eliminates surface irregularities, such as scratches, pits, and tool marks, resulting in a flawless, polished appearance. This not only enhances the aesthetic appeal of the final product but also improves its functionality, especially in industries where smooth surfaces are crucial, such as automotive, hydraulic, and pneumatic applications.Additionally, skive and roller burnishing tube processing improves dimensional accuracy. The precision achieved by this technique ensures consistent inner diameters throughout the entire length of the tube. This reliability is particularly important in industries that require tubes to meet strict tolerance standards, such as aerospace and medical applications. The uniformity in dimensions provided by this process guarantees optimal functionality and compatibility with other mechanical components, leading to enhanced overall product performance.Moreover, this advanced method of tube processing enhances mechanical properties. The cold working effect of roller burnishing increases the tube's surface hardness, resulting in improved wear resistance, fatigue strength, and corrosion resistance. These enhanced mechanical properties make skive and roller burnished tubes versatile and suitable for a wide range of industrial applications. The manufacturing industry can benefit significantly from this technology, as it allows for the production of high-quality tubes capable of withstanding demanding operational conditions.The company {} is at the forefront of skive and roller burnishing tube processing technology. With a commitment to innovation, the company has successfully developed and implemented cutting-edge equipment and techniques to deliver exceptional results. Their state-of-the-art machinery, combined with the expertise of their skilled workforce, ensures the highest level of precision and efficiency in tube processing.Furthermore, the company adheres to rigorous quality control measures, ensuring that every skive and roller burnished tube meets the highest standards. Stringent inspections throughout the manufacturing process guarantee dimensional accuracy, surface finish, and mechanical properties. This commitment to quality has earned the company a sterling reputation among various industries, making them a trusted partner for precision tube processing needs.In conclusion, skive and roller burnishing tube processing revolutionizes the manufacturing industry, offering superior surface finish, dimensional accuracy, and enhanced mechanical properties. The innovative combination of skiving and roller burnishing techniques provides manufacturers with the tools necessary to meet the demands of various industrial sectors. The company {}, with their expertise and commitment to quality, remains at the forefront of this advanced technology, contributing to the advancement of manufacturing processes and the production of high-quality products.
Revolutionizing Coal Mining: Exploring the Cutting-edge Machinery of Honing Machines
Title: Advancements in Coal Mining Machinery: Innovations in Honing Machines Revolutionize Efficiency and SafetyIntroduction:The global coal mining industry plays a crucial role in meeting our energy demands, contributing significantly to economic growth. As technological advancements continue to shape various industries, the coal mining sector is no exception. In recent times, the development of specialized machinery has transformed the mining process, enhancing efficiency, productivity, and safety for workers. This news article explores the latest innovation in coal mining machinery, specifically focusing on the advancements in honing machines, their features, and the benefits they bring to the industry.Evolution of Honing Machines in Coal Mining:Honing machines have long been an essential part of the coal mining process, facilitating the precise finishing of holes and surfaces. Traditionally, these machines required extensive manual labor and were time-consuming. However, with increasing investments in research and development, coal mining machinery manufacturers have introduced cutting-edge technology to revolutionize honing machines.Features of the Next-Generation Honing Machines:The new-age honing machines are equipped with advanced automation features, including computer numerical control (CNC) systems, intelligent software, and real-time monitoring capabilities. These advancements have significantly reduced human intervention and enhanced precision in the honing process. Additionally, the integration of robotic systems has further refined and accelerated the coal mining operations while ensuring worker safety.Improved Efficiency and Productivity:The deployment of advanced honing machines in coal mines has led to a notable increase in operational efficiency and productivity. With precisely controlled drilling and honing processes, these machines minimize the risk of errors, rework, and material wastage. The CNC systems enable operators to achieve consistent results, reducing time-consuming manual adjustments. Consequently, this allows for accelerated production cycles, ultimately boosting the overall output of coal mining operations.Enhanced Safety Measures:Safety is a paramount concern in coal mining, and the new honing machines prioritize worker well-being through automation and remote-controlled functionalities. Operators can control the machines from a safe distance, reducing exposure to hazardous working conditions. The integration of real-time monitoring systems monitors machine performance, alerting operators about any potential risks or malfunctions. This proactive approach minimizes the occurrence of accidents and injuries, creating a secure environment for the miners.Reduced Maintenance Costs:The modern honing machines are designed with durability and reduced maintenance requirements in mind. With intelligent software systems, these machines can self-monitor and predict maintenance needs, reducing downtime and associated costs. Regular software updates further enhance performance and extend the equipment's lifespan. Consequently, coal mining companies can significantly reduce their operational expenses, ensuring sustainable growth and profitability.Environmental Considerations:Another crucial aspect of the next-generation honing machines is their focus on minimizing the environmental impact of coal mining operations. These machines are designed to incorporate efficient filtration and dust control systems, preventing airborne particles and pollutants from contaminating the surrounding air. The utilization of cleaner and non-toxic drilling fluids further reduces the ecological footprint of coal mining activities. This commitment to environmental preservation aligns with global sustainability goals, making coal mining a more responsible industry.Conclusion:The continuous advancements in honing machines for coal mining have significantly reshaped the industry, setting new benchmarks for efficiency, productivity, safety, and environmental responsibility. With automation, real-time monitoring, and optimized drilling processes, these cutting-edge machines offer substantial benefits to workers and companies alike. As the coal mining sector embraces these technological innovations, the future holds promise for improved operational standards, sustainable growth, and a safer working environment.
Discover the Advancements in Cutting-Edge Machine Drilling Technology
Title: Groundbreaking New Drilling Technology Revolutionizes the IndustryIntroduction:In the ever-evolving world of drilling and machining, a groundbreaking new technology is set to revolutionize the industry. Introducing an innovative solution that combines cutting-edge techniques with unmatched precision - a culmination of years of research and development by a leading company dedicated to pushing the boundaries of engineering excellence.[Company Introduction - Removed Brand Name]:With a relentless commitment to innovation and a rich history spanning several decades, this esteemed company has emerged as a frontrunner in the field of drilling and machining. Consistently pushing the boundaries of what is deemed possible, their team of expert engineers and technicians are driven by a passion for excellence, always striving to enhance efficiency and deliver superior performance.Groundbreaking Technology:Under the company's stewardship, the development of the Deep Drill and Machine system represents a significant breakthrough in the industry. Leveraging advanced cutting-edge techniques such as computer-aided design (CAD) and computer numerical control (CNC), this unparalleled drilling technology is designed to tackle the most challenging drilling operations while delivering exceptional precision and efficiency.1. Enhanced Drilling Performance:The Deep Drill and Machine system introduces a unique amalgamation of state-of-the-art engineering, advanced materials, and cutting-edge software. This combination results in a highly robust and adaptable technology capable of drilling through the most demanding materials such as hardened steel, titanium alloys, and composite materials with seamless precision.By leveraging the power of computer-aided calculations and simulations, the system enables technicians to optimize drilling parameters, ensuring reduced vibration and enhanced stability during the drilling process. This aspect greatly minimizes tool wear, improves productivity, and ultimately leads to significant cost savings for operators.2. Unmatched Precision:Precision is the hallmark of the Deep Drill and Machine system. Equipped with intelligent sensors and real-time monitoring, the technology ensures minimal deviation from desired drilling paths, maintaining the highest standards of accuracy. The system's advanced CNC controls allow for automated adjustments and corrections, resulting in precise hole depths, angles, and tolerances.Additionally, the Deep Drill and Machine system's flexibility and adaptability facilitate customized drilling solutions for a wide range of industries. Whether it is oil and gas exploration, aerospace manufacturing, or heavy machinery production, this revolutionary technology can be tailored to meet the specific requirements of any drilling operation.3. Safety and Environmental Considerations:In an era where sustainability and environmental consciousness are paramount, the Deep Drill and Machine system addresses these concerns head-on. The technology incorporates intelligent eco-friendly features, including advanced dust collection systems and efficient cooling mechanisms.With an innovative chip management system, the Deep Drill and Machine technology minimizes waste material generation, contributing to a cleaner working environment. Furthermore, the system adheres to stringent safety protocols, ensuring optimal operator protection, and minimizing workplace accidents and injuries.Conclusion:The introduction of the Deep Drill and Machine system signifies a game-changing leap in the world of drilling and machining. Combining cutting-edge engineering, advanced software integration, and unmatched precision, this innovative technology is poised to transform drilling operations across numerous industries. With its enhanced performance, unmatched precision, and commitment to safety and sustainability, the Deep Drill and Machine system holds immense potential for revolutionizing the drilling landscape. As this groundbreaking technology becomes widely adopted, it is expected to pave the way for future advancements, bolstering the efficiency, productivity, and overall success of drilling operations across the globe.
Revolutionary Pipe Boring Machines Set to Disrupt the Construction Industry
HUGE INNOVATION IN PIPE BORING TECHNOLOGY TRANSFORMS THE CONSTRUCTION INDUSTRYIn a groundbreaking development, {} has unveiled their latest pipe boring machine that is set to revolutionize the construction industry. This state-of-the-art equipment promises unprecedented efficiency, precision, and environmental benefits, marking a significant advancement in underground infrastructure installation.{} is a renowned company that specializes in developing cutting-edge technologies for various sectors. With a vision to transform construction practices, they have successfully introduced a range of highly advanced and sophisticated machinery. The company's commitment to innovation is evident in their latest creation - a pipe boring machine that is poised to change the way pipework is installed beneath the ground.Traditional methods of pipe installation have always been labor-intensive and time-consuming, involving digging trenches and manually laying the pipes. However, this new pipe boring machine eliminates the need for such extensive excavation. It is capable of tunneling underground and creating pathways for pipes effortlessly. This groundbreaking technology offers numerous benefits over conventional methods.First and foremost, this new pipe boring machine speeds up the installation process significantly, reducing construction timelines. It works by utilizing a range of cutting-edge engineering principles that allow for quick and efficient tunneling. The machine can carve through various types of soil and rocks, ensuring a smooth and reliable process. This efficiency translates into cost savings for construction companies and reduced inconveniences for the public.Furthermore, the precision and accuracy of this pipe boring machine are unparalleled. It is equipped with advanced sensors and navigational technologies that ensure the tunnels are created with utmost precision. This eliminates the risk of damaging existing underground utilities and infrastructure, minimizing the need for expensive repairs and disruptions. The machine's ability to create tunnels with pinpoint accuracy also reduces the chances of leaks and other technical issues.The environmental benefits of this pipe boring machine are another remarkable aspect of its design. By eliminating the need for extensive excavation, it significantly reduces the amount of soil and debris removed from construction sites. This leads to a smaller carbon footprint and helps in preserving natural resources. Additionally, the machine operates quietly, minimizing noise pollution during the construction process.The machine's exceptional capabilities are a result of extensive research and development conducted by the team at {}. With a dedicated team of engineers, scientists, and industry experts, the company has brought cutting-edge technology to the forefront of the construction industry. The pipe boring machine's design incorporates the latest innovations in robotics, artificial intelligence, and materials science.{} takes great pride in their commitment to safety as well. The machine is equipped with multiple safety features to mitigate potential risks. The operators receive comprehensive training to ensure seamless operation and avoid accidents during the construction process. The company's dedication to safety has been recognized by industry experts, earning them accolades and certifications.As the construction industry continues to undergo rapid advancements, the introduction of this pipe boring machine by {} stands as a testament to their unwavering dedication to innovation and excellence. With its speed, precision, and environmental advantages, this pipe boring machine is set to transform underground infrastructure installation across the globe. Construction companies can now look forward to enhanced productivity, more efficient project completion, and a positive impact on the environment.
High-Quality SkivingLRoller Burnishing Tools for Precision Metalworking
Skiving Roller Burnishing Tools Elevate Surface Finishing Efficiency and Precision in MetalworkingIn today's manufacturing industry, efficiency and precision are the key drivers for success. With the demand for high-quality products increasing rapidly, industries like automotive, aerospace, and defense are constantly on the lookout for innovative solutions. One such groundbreaking tool that has significantly revolutionized surface finishing is the Skiving Roller Burnishing Tool.Developed by a leading company that specializes in cutting-edge metalworking solutions, the Skiving Roller Burnishing Tool has garnered immense popularity due to its exceptional performance and unmatched efficiency. This revolutionary tool is specifically designed to enhance surface finishes and improve dimensional accuracy, reducing manufacturing time while maintaining superior quality.Traditionally, achieving high-quality surface finishes was a complex and time-consuming process. Machining techniques such as honing, grinding, and lapping were commonly used, but they often presented limitations like high costs, excessive material removal, and extended machining times. However, with the introduction of Skiving Roller Burnishing Tools, metalworking processes have now evolved to an entirely new level.The Skiving Roller Burnishing Tool's success lies in its innovative design and utilization of advanced technologies. The tool features a cutter head equipped with multiple rolls or blades that rotate at a high speed while the workpiece remains stationary. As the tool moves along the workpiece, the rolls smooth and compress the surface, resulting in an exceptional finish and superior dimensional accuracy.What sets the Skiving Roller Burnishing Tool apart from other traditional machining techniques is its ability to produce mirror-like surface finishes with ultra-precise tolerances. This tool eliminates the need for secondary operations, saving significant time and cost in the manufacturing process. It also minimizes material waste by reducing excess material removal, making it an environmentally friendly option.The Skiving Roller Burnishing Tool's versatility is yet another reason for its widespread adoption. It can effectively work on various materials, including steel, aluminum, copper, and alloys, making it a suitable tool for different industries. From automotive engine components to hydraulic cylinders, this tool has proved its effectiveness across multiple applications.Furthermore, the Skiving Roller Burnishing Tool's simplicity makes it user-friendly and easy to integrate into existing manufacturing processes. By utilizing this tool, manufacturers can reduce the number of machining steps required, streamline their operations, and boost productivity. Its efficiency has been estimated to be three to five times higher than conventional machining techniques.The company behind the Skiving Roller Burnishing Tool is renowned for its commitment to excellence and continuous innovation. With a strong emphasis on research and development, they have developed a wide range of cutting-edge metalworking solutions that cater to various industry needs. By incorporating advanced technologies, the company has successfully propelled the manufacturing industry towards enhanced efficiency and precision.In conclusion, the Skiving Roller Burnishing Tool has revolutionized surface finishing in the metalworking industry. With its ability to produce exceptional finishes and superior dimensional accuracy, this innovative tool has significantly reduced manufacturing time and cost while maintaining high-quality standards. Its versatility and ease of integration have made it a game-changer for various industries, propelling them towards increased productivity and success. With the continuous commitment to innovation by the leading company behind this tool, the future of metalworking holds even more promising advancements.